视频专区
Current Location:HOME
- Author:
- Source: 北京SMT专业委员会
- Date: 2016-11-08
- Views: 6415Times
作者:公安部第一研究所 顾霭云
摘要:目前我国军工电子产品普遍存在有铅和无铅元器件混装焊接的现象,有铅和无铅混用时,可能会发生材料之间、工艺之间、设计之间不相容等问题,影响电子产品的可靠性。军工产品可靠性是第一位,既要保证焊点质量,又要保证不损坏元器件和印制板。本文通过对有铅和无铅混装焊接可能发生的不相容问题分析,对高可靠产品有铅和无铅混装工艺的质量控制方案提出一些建议。文章中的观点供参考并与同行共同讨论。
关键词:有铅焊料、有铅焊接、无铅焊料、无铅焊接、有铅元器件、无铅元器件、有铅和无铅混装、物料管理、可靠性、材料相容性、工艺相容性、设计相容性。
虽然电子产品无铅化在国际上已经有近20年的经验,国内也推行近10年了,目前在消费类、通信类等领域已经比较普遍地应用了无铅技术,总体来看也没有发生太大的可靠性问题。但是由于无铅焊点蠕变大,无铅焊料是“高锡”焊料。高锡带来的是高温、表面张力大、黏度大、浸润性差、工艺窗口小等问题,高温又会带来工艺上的难度,可能会导致的元件和电路板降级甚至损坏。另外,焊接温度越高金属间化合物生长速度越快,界面微孔、空洞多,金属间化合物是脆性的,无铅焊点比Sn-Pb焊点更硬也传递了更大的应力,这些问题都会影响无铅产品的长期可靠性。到目前为止,世界各国研究机构对无铅焊接可靠性等方面还没有统一的认识,无铅产品的长期可靠性在业内还存在争议,并确实存在不可靠因素,这也是国际上对军事、航空航天、医疗等高可靠要求领域的电子产品获得豁免的主要原因之一。由于汽车产品涉及人身安全,欧盟在2010年2月23日颁布了对ELV(End-of-Life Vehicle欧盟报废车辆指令)附件二的更新,新的ELV附件二规定汽车产品的含铅焊锡禁用期限被推迟1~5年(更新的主要内容:电子、电气元器件焊接到电路板上所使用的含铅焊锡,可延期到2016年1月1日;电解电容/铝电容引脚上的铅/锡,可延期到2013年1月1日;85%及以上的铅合金高温焊锡,可延期到2015年1月1日)。从期限被推迟可以看出高可靠产品无铅化的发展和替代锡铅的困难。虽然国际上高可靠产品获得豁免,而目前我国没有豁免政策,那么我们军工等高可靠领域怎么解决?这是近年来业界十分关心的问题。
从理论上来讲,就焊点来说,焊料、元器件焊端、PCB表面镀层全部是锡铅,或全部是无铅的相容性是最好的。目前,如果采用无铅焊接,可以买到所有的无铅元件。对于大多数民用、通信等领域,由于使用环境应力小、不恶劣,应用无铅焊接是没有问题的。对于军工等高可靠领域,其长期可靠性存在不确定因素,可能会有风险的。因此,建议军工等高可靠领域暂时还是采用有铅焊接相对比较安全一些。
目前的问题是有铅工艺买不全有铅元件,有铅工艺遇到85%甚至90%以上无铅元件,因此,我国军工电子产品普遍存在有铅和无铅元器件混装焊接的现象——目前大多采用有铅焊料焊接有铅和无铅元器件。本文对有铅和无铅混装焊接可能发生的不相容问题进行了较详细的分析,并对高可靠产品有铅和无铅混装工艺的质量控制方案提出一些建议。
一、有铅和无铅混装焊接可能发生的不相容问题分析
军工产品可靠性是第一位,既要保证焊点质量,又要保证不损坏元器件和印制板。采用有铅焊料焊接有铅和无铅元器件。有铅和无铅混装焊接时有85%甚至90%以上无铅元件,无铅元件的焊端镀层大多是镀纯Sn的,容易形成Sn须;采用有铅焊料焊接有铅和无铅元器件时,有铅焊料焊接有铅元器件时材料和熔点温度都是相容的;有铅焊料焊接无铅元器件时,Sn-Pb焊料的熔点183℃,无铅元件焊端镀层Sn熔点为232℃,无铅BGA焊球Sn-Ag-Cu熔点217℃。由于无铅元件焊端镀层和焊球的熔点高于Sn-Pb焊料的熔点,因此,焊接时需要提高焊接温度,高温可能损坏有铅元器件和PCB基板,特别是对潮湿敏感元器件的影响不可忽视;另外,PCB和工艺设计时,基板材料、PCB焊盘涂镀层材料选择不当也会发生材料不相容等等问题。
如果设计、工艺、采购、管理不当就有可能会发生材料之间、工艺之间、设计之间不相容问题,影响电子产品的长期可靠性。
1、锡晶须问题
晶须(Whisker)是指从金属表面生长出的细丝状、针状形单晶体,它能在固体物质的表面生长,易发生在Sn、Zn、Cd、Ag等低熔点金属表面。通常发生在0.5~50μm、厚度很薄的金属沉积层表面。典型的晶须直径为1~10μm,长度为1~500μm。过长的锡晶须可能导致短路,引发电子产品可靠性问题,见图1。
图1 锡晶须增长会引发电子产品可靠性问题
由于镀Sn工艺简单、成本比较低,因此,目前无铅元件焊端和引脚表面采用镀纯Sn工艺比较多,但由于Sn表面容易氧化形成很薄、厚度不均匀的氧化层。镀Sn时在Cu表面会生成金属间化合物Cu6Sn5,Cu6Sn5的膨胀系数比较大,加电后或温度变化时Cu6Sn5对Sn镀层产生压力,在不均匀处会把Sn推出来,形成Sn须。在高温、潮湿和有负载震动等应力的环境里,Sn晶须的生长速度会加快,过长的晶须如发生在窄间距QFP等元件引脚上容易造成短路,晶须可能立即生长,也可能要经过几千小时的潜伏期后才开始生长出来。使长期电气可靠性存在隐患。
针对锡晶须问题,业界做了许多研究,目前已经有一些有效抑制Sn晶须生长的措施,主要有以下措施:
⑴ 镀层合金化
在Sn中添加Pb、Ag、Bi、Cu、Ni、Fe、Zn等金属元素可以有效抑制Sn晶须生长。目前大多采用Sn-Ni镀层,也有采用Sn-Ag-Cu、Sn-Ag和 Sn-Cu的。日本、韩国的某些无铅元件焊端还有采用Sn-Ag-Bi、Sn-Bi镀层。
⑵ 中间镀层
在镀Sn前先镀一层其它金属元素作为阻挡层,通常采用Ni。一般先镀Ni(>1μm)再镀Sn(1~3μm),中间形成金属间化合物Ni3Sn4,由于Ni3Sn4比较稳定,不容易对Sn镀层产生挤压。
⑶ 镀暗Sn(不要镀亮Sn,亮Sn 容易生长Sn须)
⑷ 增加镀Sn厚度至8~10μm
⑸ 热处理
•退火(在烘箱中烘150℃/2h或170℃/1h)
•熔化、回流
⑹ 采用“敷形涂覆”工艺(俗称“三防”工艺)来解决
2、Sn-Pb焊料与无铅元件镀层材料不相容
从形成焊点的3个要素(焊料、元器件焊端、PCB表面镀层)来看,在传统的Sn-Pb焊接时,焊料是Sn-Pb,元器件焊端、PCB表面镀层大多也是Sn-Pb镀层,因此,焊接时焊料合金与被焊接金属之间的相容性非常好。
无铅元器件端表面镀层除了镀纯Sn外,还有镀Sn-Ag-Cu、Ni-Au、Ni-Pd-Au、Pd-Ag、Sn-Cu、Sn-Ag-Bi、Sn-Bi等合金层的。因此,在焊料与元件这一侧,可能会发生多种不同的界面反应;它们形成最佳金属间化合物的温度、时间等条件也有所差别;生成的金属间化合物的结构、厚度、强度、可靠性也有所不同了。在同一块组装板上,如果有一个元件、甚至只有一个焊点不相容,都可能造成整个电路的故障。下面举两个例子。
⑴ Sn-Pb焊料与Sn-Bi镀层不相容
焊料中的Pb与Sn-Bi镀层中的Bi在引脚或焊端界面形成Sn-Pb-Bi(熔点93℃)的三元共晶低熔点层、焊接后在焊点与焊端交界处会加剧分层Lift-off(如图2所示),使焊点浮起(焊缝起翘),严重时甚至会将PCB焊盘一起剥离开,导致焊接强度劣化。
图2 焊缝起翘现象(Lift-off)
⑵ Pd-Ag和Pd-Au端头镀层的元件回流焊时,由于浸析现象,容易在高温下过早溶解在焊料中,或者出现气泡,产生空洞,导致焊点接触不良。
3、高温可能损坏元器件封装体及内部连接、损坏PCB基材
传统的Sn-Pb焊料焊接有铅元器件时,其焊接温度一般不超过240℃,恰好在有铅元器件和PCB基材能够耐受的温度范围内。但是,有铅和无铅混装焊接时有大量的无铅元器件,无铅元件的焊端镀层和焊球的熔点高于Sn-Pb焊料的熔点,为了保证焊料与元件之间的连接强度,必须提高焊接温度,因此,采用有铅焊料焊接有铅和无铅元器件时,也存在高温的问题。高温可能损坏元器件和PCB基板。
例如,陶瓷电阻器和特殊的电容器对温度曲线的斜率(温度的变化速率)非常敏感,由于陶瓷体与PCB的热膨胀系数(CTE)相差较大(陶瓷为3~5ppm/℃,PCB为18ppm/℃左右),在焊点冷却凝固时容易造成元件体和焊点裂纹。元件开裂现象与CTE的差异、温度、元件的尺寸大小成正比。0201、0402、0603小元件一般很少开裂,而1206以上的大元件发生开裂失效的机会较多。又如,铝电解电容对温度极其敏感。有些钽电容只能承受183℃以上不能超过60s,240℃不能超过10s;一些小型表面贴装变压器的骨架不耐高温,要求220℃不能超过10s;有的有铅器件230℃不能超过10s;一些热敏元件如聚合物开关(PWS)在再流焊后阻值会发生变化,在温度降低后仍不能恢复。因此,需要注意对元器件的选择,避免高温对元器件损伤导致失效。图3 是高温损坏元件和PCB基板的例子。
(a)元件开裂 (b)连接器件损伤 (c)基板内部树脂损伤
图3 高温损坏元件和PCB基板
4、高温对湿度敏感器件(MSD)的不利影响
湿度敏感器件(MSD)主要指非气密性(Non-Hermetic)器件。包括:
塑料封装;
其他透水性聚合物封装(环氧、有机硅树脂等);
一般IC、芯片、电解电容、LED等。
采用有铅焊料焊接有铅和无铅元器件时,需要提高焊接温度,也存在高温问题。因此,还必须高度重视器件的潮湿敏感度问题。吸潮的器件在再流焊过程中由于水蒸气膨胀,使水蒸气压随温度升高而上升,对已经受潮的器件都会造成损坏的威胁。连接器和其他塑料封装元器件(如PBGA、QFP等)在高温时失效明显增加,主要是分层、爆米花、变形、开裂等。
(a)塑封器件封装开裂失效 (b)器件内部封装失效 (c)PBGA器件基板起泡
图4 受潮的湿度敏感器件受高温损坏
IPC与JEDEC共同制定的MSD潮湿敏感等级标准J-STD-033A是按照有铅元件220℃的焊接温度制订的,根据经验粗略统计,焊接温度每提高10℃,湿度敏感器件(MSD)的湿度敏感等级(MSL)提升1级,可靠性随之下降1级。如果Sn-Pb器件定级为MSL3,有铅焊料焊接有铅和无铅元器件时至少提高10~15℃,湿度敏感等级将提升到MSL4~MSL5。因此,再流焊工艺中要特别注意对湿度敏感器件(MSD)的管理,解决措施是对湿度敏感元器件(MSD)按照要求进行管理、存储和使用,尽量降低峰值温度,对已经受潮的潮湿敏感元器件进行
去潮烘烤处理。图4 是受潮的湿度敏感器件受高温损坏的例子。
5、PCB焊盘涂镀层ENIG(Ni/Au)的金脆和黑焊盘问题
ENIG(Ni/Au)俗称水金板,是化学镀Ni/闪镀金Au工艺。Ni层>3µm(一般5~7µm),Au层一般0.05~0.15µm,ENIG(Ni/Au)镀层表面平整、耐磨、接触电阻小、抗氧化,适用于高密度SMT板的双面再流焊工艺,是军工和高可靠产品PCB常选用的焊盘表面镀层。薄Au层在焊接时迅速熔于焊料中,露出清洁新鲜的Ni与熔融焊料中的Sn形成Ni3Sn4,使焊点更牢固。少量Au熔于锡中不会引起焊点变脆,Au层只起保护Ni层不被氧化的作用。图5是Sn系焊料与Ni/Au(ENIG)焊接后钎缝组织的扫描电子显微镜(SEM)照片。从图中可以看出,在Ni焊盘这一侧,Ni与焊料之间的金属间化合物主要是Ni3Sn4,在焊料一侧主要是AuSn4。Ni-Sn化合物比较稳定,Ni-Sn界面反应层与Sn-Cu反应层相比,反应速度比较慢一些,金属间化合物的厚度也相对薄得多,因此Ni-Sn合金的连接强度较好;但是Au能与焊料中的Sn形成Au-Sn间共价化合物AuSn4、AuSn2、AuSn(主要是AuSn4)。AuSn4不是我们需要的结合层。在焊点中金的含量超过3%会使焊点变脆,过多的Au原子替代Ni原子,因为太多的Au溶解到焊点里,无论与Sn-Pb还是与Sn-Ag-Cu焊接,都将引起“金脆”。所以一定要限定Au层厚度,通常用于焊接的Au层厚度≤1µm(钎焊时控制在0.05~0.15µm)。
图5 Sn系焊料与Ni/Au(ENIG)的钎缝组织
另外印制板加工时,如果ENIG(Ni/Au)的工艺参数控制不好,Ni被酸腐蚀或氧化,会造成“黑焊盘”现象。
关于ENIG 的“黑焊盘”(Black Pads in ENIG Finishes)问题说明如下。
图6是“黑焊盘”现象。黑焊盘是PCB制造厂的问题,有铅焊接也存在这个问题。黑焊盘处用手指一推,元件就会掉下来。
图6 “黑焊盘”现象
⑴ “黑焊盘”(Black Pads in ENIG Finishes)现象的产生原因
① 金镀层结构不够致密,表面存在针孔和裂缝,空气中的水汽容易进入,造成镍镀层氧化。
② 镍镀层磷含量偏高或偏低,导致镀层耐酸腐蚀性能差,易发生腐蚀变色,出现“黑焊盘”现象,使镀层可焊性变差。一般建议P 含量控制在7~9%,pH值为3~4较好。
③ 镀镍后没有将酸性镀液清洗干净,长时间 Ni被酸腐蚀。
④ 作为可焊性保护性涂覆层的Au镀层在焊接时会完全溶蚀到焊料中,而被氧化或腐蚀的Ni镀层由于可焊性差不能与焊料形成良好的金属间合金层,最终导致虚焊或焊点强度不足,使元件从PCB上脱落。
⑵ 关于富磷现象的解释
① 在化学镀Ni-P(镍-磷)的情况下,Ni向Sn一侧扩散,在焊料一侧形成较厚的Ni3Sn4(见图7左),造成Ni-P合金中Ni欠缺、P剩余,因此可以理解为形成了富P的Ni层(见图7右)。
② Ni3Sn4和富P的Ni层界面附近容易形成空洞(见图7右),空洞会降低界面的连接强度。
因此,高可靠产品选择ENIG(Ni/Au)板时,对PCB制造厂要提出质量控制的要求,
图7 Ni镀层与Sn合金界面的模型
6、有铅焊料与无铅PBGA、CSP混用必须提高焊接温度
有铅焊料与无铅PBGA、CSP混用时,如果采用有铅焊料的温度曲线,焊点连接可靠性是最差的。这是由于有铅焊料与无铅焊球的熔点不相同,有铅焊料熔点低先熔,而无铅焊球不能完全熔化,容易造成PBGA、CSP一侧焊点失效的缘故。
图8是有铅焊料与无铅焊球混用示意图。从图中可以看出,无铅PBGA、CSP的焊球一般是Sn-Ag-Cu合金,熔点高(217℃),Sn-37Pb焊料的熔点低(183℃),如果采用Sn-37Pb焊料的温度曲线,一般峰值温度在210~230℃。假设峰值温度为220℃,再流焊时,当温度上升到183℃时印刷在焊盘上的Sn-37Pb焊膏开始熔化,此时无铅PBGA的Sn-Ag-Cu焊球还没有熔化;当温度上升到220℃时,按照有铅工艺就要开始降温、结束焊接了,此时无铅焊球刚刚熔化。虽然Sn-Ag-Cu合金标称的熔点为217℃,但实际上Sn-Ag-Cu合金并不是真正的共晶合金,固相线与液相线的温度范围是216~220℃,因此,有铅工艺冷却凝固结束焊接的温度恰好是无铅Sn-Ag-Cu焊球刚刚熔化之时,并处于固、液相共存的浆糊状态。焊球熔化时由于器件重力的作用开始下沉,在器件下沉过程中稍有震动或PCB微量变形,便使PBGA、CSP元件一侧原来的焊接界面结构遭破坏,又不能形成新的界面金属间合金层,最终造成PBGA、CSP一侧焊点失效,如图9所示。因此有铅焊料与无铅焊球混用时,采用有铅焊接工艺的质量最差。解决上述问题的措施有两条。
⑴ 通过提高焊接温度的方法解决
必须提高焊接温度到235℃左右,使器件一侧的焊球实现二次回流,这样可以使器件一侧的焊球合金充分熔化,在焊球与器件的焊盘之间生成新的金属间化合物,形成良好的电气与机械连接。
⑵ 还要注意其他有铅元件能否承受高温
图8 有铅焊料与无铅焊球混用示意图 图9 PBGA、CSP在元件一侧的界面失效
7、电气可靠性
通常同一块PCB要经过回流焊、波峰焊、返修等工艺,很可能形成不同的残留物,在潮湿环境和一定电压下,可能会与导电体之间发生电化学反应,引起表面绝缘电阻(SIR)的下降。如果有电迁移和枝状结晶生长出现,将发生导线间的短路,造成电迁移(俗称“漏电”)的风险。图10是电迁移造成的树枝状结晶的例子。
为了保证电气可靠性,需要对不同免清洗助焊剂的性能进行评估,同一块PCB要尽量采用相同的助焊剂,或进行焊后清洗处理。
图10 电迁移造成的树枝状结晶
二、高可靠产品有铅和无铅混装工艺质量控制方案的建议
根据以上分析、讨论,可见:采用有铅焊料焊接有铅和无铅元器件工艺,如果设计、工艺、采购、管理不当就有可能会发生材料之间、工艺之间、设计之间等不相容问题,影响高可靠电子产品的长期可靠性。主要有锡晶须问题、Sn-Pb焊料与无铅元件镀层材料不相容、高温可能损坏元器件封装体及内部连接、高温可能损伤PCB基材、高温对湿度敏感器件(MSD)的不利影响、PCB焊盘涂镀层ENIG(Ni/Au)的金脆和黑焊盘问题、有铅焊料与无铅PBGA、CSP混用必须提高焊接温度、电气可靠性等等。另外,BGA器件有铅无铅混合球的长期可靠性问题也被提出了,目前还没有研究结果。
从以上的不可靠因素还可以看出,例如锡晶须、器件和PCB基材的内部损伤、金脆和黑焊盘、电气可靠性等都是隐蔽的缺陷。隐蔽的缺陷不容易被发现,因此往往不被重视。它们的可靠性都是随着时间的推移,在使用过程中由于受到机械震动、跌落或电路板被弯曲,受到环境温度、工作温度的循环热应力等因素的影响逐渐削弱的。这些隐蔽的缺陷增加了高可靠电子产品长期可靠性的不确定性。
因此,我们必须从产品设计开始就考虑到材料、工艺、设计之间的相容性;充分考虑散热问题;仔细地选择PCB板材、焊盘表面镀层、元件、焊膏及助焊剂等;比有铅焊接时更加细致地进行工艺优化和工艺控制;更加严格细致地进行物料管理。
下面对军工等高可靠电子产品,有铅和无铅混装工艺质量控制提出如下建议,供参考并与同行共同讨论。
1、暂时不建议采用无铅工艺,建议采用有铅焊料焊接有铅和无铅元器件工艺
如果决定实施无铅工艺,建议选择Sn-3.5 Ag二元共晶合金。其主要理由是Sn-3.5 Ag合金已在某些高可靠电子领域应用了很长时间,已经完成大量测试,并且已被高可靠领域广泛接受。同时,一定要做可靠性认证。
2、严格物料管理
虽然目前的混装工艺采用有铅焊料焊接有铅和无铅元器件,但是遇到含Bi无铅元器件时需要采用无铅焊料焊接,生产线还可能存在两种焊料,因此,元件和材料管理很重要。
⑴ 物料管理的一般要求
① 元器件采购技术要求。对采购部门进行ROHS培训,加强对上游供应商的管理。
② 备料。首先要注意元器件的焊端材料是否无铅,如果是无铅元器件,一定要弄清楚是什么镀层材料,特别是BGA\CSP和新型封装的器件,如QFN等。BOM表上必须标注的内容包括焊端表面镀层材料、最高耐受温度和时间、潮敏度等级。
③ 标识和标签。应给无铅元器件做无铅标识和标签。
④ 规定无铅元器件编号方式。
⑤ 识别。对生产线操作人员进行培训,提高对无铅标识、标签的识别能力。并自觉遵守无铅管理制度
⑥ 材料管理自动化。生产过程中可以用手工扫描条形码标签,也可以通过贴片机上的RFID智能供料器识别,实现材料管理自动化。
⑦ 生产线设置验证。为了防止贴片机上装错元件,从而造成不必要的损失,应使生产线的设置通过手工、半自动或闭环验证。
⑧ 可追溯性与材料清单。可追溯性要求对每一块组装板编一个独一无二的序号,然后将这块组装板上所有的元器件及组装工艺的信息记录在案,一旦出现问题,很容易追溯到问题的根源。这种管理是当前最先进的方法,但需要很大的投资。
⑨ 无铅元器件、工艺材料的储存。 在储存方面,企业可以考虑设立单独的无铅工艺材料、无铅元器件、用于无铅的模板和工具的仓库,或从现有的仓库划出相当的空间用于无铅物料、工具等物品的储存。
⑩ 无铅的专用工具。必须具备无铅专用模板、烙铁或焊台、镊子、刷子等工具,并做标识。
设立无铅手工焊接的专用工位。
⑿ 加强静电防护与管理措施
⒀ 对湿度敏感器件(MSD)采取正确的控制措施
⑵ 设计人员在BOM表上必须标注的内容
•元器件的内引线材料、焊端表面镀层材料;
•最高耐温及最高温度下的耐受时间;
•最大升温和降温斜率;
•潮敏度等级。
⑶ 工艺人员根据设计文件进行工艺控制和设计温度曲线
•例如对潮敏元件、含Bi元件的控制等
⑷ 操作人员要按照正确的工艺方法实施
3、用有铅焊料焊接有铅和无铅元器件的原则
⑴ 焊接材料的选择
① 焊料合金:选择Sn-37Pb共晶合金或62Sn-36Pb-2Ag
合金成分是决定焊料熔点及焊点质量的关键参数,应尽量选择共晶或近共晶合金。选择共晶合金具有以下好处:
•共晶合金的熔点最低,焊接温度也最低,焊接时不会损坏元件和印制板;
•所谓共晶焊料就是由固相变液相或由液相变固相均在同一温度下进行,降温时当温度降到共晶点时,液态焊料一下子全部变成固相状态,因此焊点凝固时形成的结晶颗粒最小,结构最致密,有利于提高焊点强度;
•共晶合金在冷却凝固时只要降到共晶点温度,就会立即从液相变成固相,因此共晶合金在凝固过程中没有塑性范围,有利于焊接工艺的控制。合金凝固温度范围(塑性范围)对焊接的工艺性和焊点质量影响极大。塑性范围大的合金,在合金凝固、形成焊点时需要较长时间,如果在合金凝固期间PCB和元器件有任何震动(包括PCB变形),都会造成“焊点扰动”,有可能会发生焊点开裂,使电子设备过早损坏。
② 焊膏的选择
•免清洗产品选择免清洗焊膏
•需要清洗和需要做三防工艺的产品应选择溶剂清洗焊膏,或水清洗焊膏
③ 助焊剂的选择
助焊剂在焊接中起着十分重要的作用。它能够去除被焊金属表面的氧化物;防止焊接时焊料和焊接表面的再氧化;降低焊料的表面张力,增强润湿性;有利于热量传递到焊接区。助焊剂的种类非常多,据统计大约有几百种规格。常用助焊剂有4类:松香型助焊剂、水溶性助焊剂、低固含量的免清洗助焊剂、无VOC助焊剂。
助焊剂的性能直接影响焊接质量,如果选择不当,不仅起不到助焊作用,反而会造成机械强度降低、电化学腐蚀、电迁移等可靠性问题。因此,正确选择助焊剂十分重要。助焊剂通常与焊料匹配使用,要根据焊料合金,根据不同的工艺方法,同时还要根据被焊的元件引脚、PCB焊盘的涂镀层材料、金属表面氧化程度,以及产品对清洁度和电性能的具体要求进行选择。
•一般情况下,军用及生命保障类如卫星、飞机仪表、潜艇通信、保障生命的医疗装置、微弱信号测试仪器等电子产品必须采用清洗型的助焊剂。
•通信类、工业设备类、办公设备类、计算机等类型的电子产品可采用免清洗或清洗型的助焊剂。
•一般家用电器类电子产品均可采用免清洗型助焊剂,或采用RMA(中等活性)松香型助焊剂,可不清洗。
•手工焊接和返修时一定要选择与再流焊、波峰焊时相同的助焊剂。
•水溶性焊剂的可焊性非常好,常用于高可靠和金属表面氧化较严重的场合。但由于其残留物的腐蚀性很大,因此在使用过程中,需经常添加专用的稀释剂调节活性剂浓度,以确保良好的焊接效果。并要求焊后2小时内必须进行清洗。
⑵ 对PCB设计的要求
① PCB基板材料的选择
PCB基板材料主要根据电子产品的性能指标、使用环境、焊接温度来选择的。
•焊接温度240℃以下的产品,采用FR4环氧玻璃纤维基板;
•焊接温度240~250℃的产品,可选择高Tg(150~170℃)FR-4;
•高可靠及厚板,焊接温度250℃以上的产品,采用FR-5;
•使用环境温度较高或挠性电路板采用聚酰亚胺玻璃纤维基板;
•对于散热要求高的高可靠电路板采用金属基板;
•对于高频电路则需要采用聚四氟乙烯玻璃纤维基板。
② PCB焊盘涂镀层的选择
PCB焊盘涂镀层是根据焊料和工艺选择的,优先选择与传统有铅工艺相容的镀层材料。
(a)一般组装密度:选择Sn-Pb热风整平法(HASL),因为HASL与Sn-Pb焊料最相容。
(b)高组装密度:选择化学镀镍-金(ENIG)。化学镀Ni-Au是指PCB连接盘上化学镀Ni(厚度≥3μm)后再镀上一层0.05~0.15μm的薄金。在选择ENIG后,一定要保证ENIG的工艺质量。
(c)高可靠产品:可选择电镀镍金,Ni镀层厚度3~6µm ,Au层厚度0.05~0.15μm。
(d)特殊情况还可以选择Ni-Pd-Au镀层。Ni层厚度3~6µm ,Pa层厚度0.1~0.5µm ,金层厚度0.02~0.1µm。
③ 元器件的选择
•尽量选择有铅元件;
•对于那些镀Sn焊端的有引脚和无引脚无铅元件,因为Sn与Sn-Pb焊料焊接时是兼容的,至于镀Sn焊端的锡须问题,还可以通过对组装板的“敷形涂覆”工艺(俗称“三防”工艺)来解决,但是要特别警惕混入镀Sn-Bi元件。
•如果有Sn-Bi元件,可以采用Sn-Ag-Cu焊料手工焊接(必须设立无铅手工焊接的专用工位,专用工具,并做标识)。
•对于无铅PBGA、CSP,一般情况可以通过适当提高焊接温度解决,使器件一侧的焊球合金充分熔化,在焊球与器件的焊盘之间形成良好的电气与机械连接。
④ PCB焊盘设计
按照国际、国内行业、企业高可靠产品设计规范
⑶ 组装方式与工艺流程设计设计
首先要确定组装方式及工艺流程。组装方式与工艺流程设计合理与否,直接影响组装质量、生产效率和制造成本。
① 组装方式与工艺流程、焊接方式设计原则
•选择最简单、质量最优秀的工艺
•选择自动化程度最高、劳动强度最小的工艺
•工艺流程路线最短
•工艺材料的种类最少
•选择加工成本最低的工艺
② 工艺流程及焊接方式设计
主要根据印制板的组装密度和本单位SMT生产线设备条件。高可靠产品可作如下考虑。
•尽量采用再流焊方式,不采用或少采用波峰焊、手工焊工艺。因为再流焊工艺简单、质量优秀、自动化程度高、工艺流程路线短、工艺材料的种类少、加工成本低。
•当通孔元件的比例只占元件总数的10%~5%甚至以下时,可以考虑选择通孔元件再流焊工艺。通孔元件再流焊工艺与波峰焊工艺相比具有工艺简单、焊接质量好、成本低等优点。
•可以采用选择性波峰焊技术替代手工焊接。传统波峰焊工艺是PCB的焊接面(辅面)完全浸入液态焊料中,而在选择性波峰焊,仅有部分特定区域与焊锡波接触。选择性波峰焊技术比手工焊接的效率高、质量好。
•激光焊接也是最近几年国际上高可靠电子产品流行的焊接方法,激光焊接技术是非接触式焊接,不会伤害元件和印制板,温度控制精确,焊接质量好。
⑷ 再流焊工艺控制
① 运用焊接理论,正确设置和优化再流焊温度曲线
混装焊接时,升温区、预热区、助焊剂浸润区、峰值温度和液相时间等参数设置介于有铅(Sn-37Pb)和无铅(Sn-3.0Ag-0.5Cu)之间。
图11是用63Sn-37Pb焊料焊接有铅和无铅元器件混装再流焊温度曲线示意图。
110℃ 130℃ 155℃ 185℃ 240℃ 260℃ 90℃
PCB入口 出口
100℃ 130℃ 165℃ 195℃ 240℃ 260℃ 90℃
传送带速度:60cm/min
温度℃
焊接时间
峰值温度
230~245
183
150 1.2~3.5℃/s
2~4min
100
冷却区
<2℃/s 0.55~1℃/s -2~-4℃/s
升温区 预热区 回流区 时间min
60~90s 60~120s 20~50s 50~80s
助焊剂浸润区
(快速升温区)
图11 用63Sn-37Pb焊料焊接有铅和无铅元器件混装再流焊温度曲线示意图
下面结合图11介绍如何运用焊接理论,正确设置和优化混装再流焊温度曲线。
在实施再流焊过程控制之前,必须了解再流焊的焊接机理,确定明确的技术规范。
确定再流焊技术规范的依据:首先是焊膏供应商提供的温度曲线,因为焊膏中的合金成分决定了熔点,助焊剂的成分、性质决定了活化温度和活化温度范围;其次是元器件和PCB材料能承受的最高极限温度及其他要求;表面组装板搭载元器件的密度、元器件的大小以及有无CBGA、CCGA等特殊元器件;还要根据设备的具体情况,例如加热区长度、加热源材料、再流焊炉构造和热传导方式、排风量的大小、温度传感器的实际位置等因素来确定各温区的设置温度。有时环境温度对炉温也有影响,特别是加热温区短、炉体宽度窄的再流焊炉,在炉子进出口处要避免对流风。
再流焊技术规范一般包括以下内容:
•最高的升温速率
从室温到100℃为升温区,也称干燥区、预热1区。升温速度一般控制在<2℃/s,或160~170℃前的升温速度控制在1~2℃/s。
在升温区,随着温度升高,焊膏的黏度下降,焊膏塌落、覆盖焊盘,将焊盘、元器件引脚与氧气隔离;另外,焊膏中的溶剂、气体蒸发掉。溶剂的沸点一般在80℃左右,如果升温速度过快,容易使焊膏合金中的微粉(微小颗粒)随溶剂挥发而飞溅到PCB焊盘以外的地方,回流时造成微小焊锡珠;如果升温速度过慢,溶剂等气体挥发不干净,回流时也会造成飞溅。另外,有些潮湿敏感元件升温速率要求控制在0.5~1.5℃/s,一般不超过2℃/s,因此,需要控制升温区的升温速度。
•预热温度和时间
100~150(或170)℃为预热区,也称预热2区或保温区。预热区的时间约60~120s。
在预热区,PCB和元器件得到充分预热。缓慢升温、充分预热的作用是避免元器件及PCB突然进入回流区,由于受热太快而损坏元器件、造成PCB变形;充分预热的另一个作用是减小PCB各处及大小元器件的温差Δt,有利于降低回流时大小元器件的焊接温差。但是,如果预热温度太高、时间过长,容易使焊膏中的助焊剂提前被全部烧掉,造成焊料合金融化时助焊剂完全丧失活性,严重时会使合金粉末受高温再氧化,影响焊接质量。因此,预热温度不能超过助焊剂的活化温度(有铅焊膏中助焊剂的活化温度一般为174℃)。复杂的、大尺寸、厚的热容量大的多层板,组装密度高、元件尺寸和质量大的组装板,预热温度需要高一些、预热时间长一些,回流焊时吸热就少一些,有利于降低大小元件的Δt。
•助焊剂浸润区(活化)温度和时间
150(或174)~183℃为助焊剂浸润区,或称为快速升温区。理想的升温速度为1.2~3.5℃/s,最多控制在0.55~3.2℃/s,大约20~50s(有铅焊接时还可以接受)。
在助焊剂浸润区,焊膏中的助焊剂润湿焊盘、元件焊端,并清洗氧化层。我们知道,焊膏中助焊剂的主要成分是松脂(树脂)、活化剂、溶剂和少量其他添加剂。松脂的活化温度在174℃左右,恰好在Sn-37Pb合金熔点(183℃)之下。所谓“活化”就是发生分解反应,在活化温度下松香酸能够起到清洗氧化铜的作用。
正确控制助焊剂浸润区的温度和时间对提高焊点质量具有重要意义。因为钎焊焊接只能在清洁的金属表面进行。此阶段的作用是清理焊件的被焊界面,把界面的氧化膜及附着的污物清除干净。助焊剂浸润区的温度和时间是根据焊膏中助焊剂的活化温度来确定的。如果助焊剂浸润区的温度太低、时间太短,不能在合金熔化前充分清洗焊件表面的氧化层,就会造成合金熔化时由于反应太剧烈而产生焊液飞溅,形成锡珠、气孔;如果助焊剂浸润区的温度过高、时间过长,又会使助焊剂提前失效,影响液态焊料的浸润性,影响金属间合金层(或称为金属间化合物)的生成。
总之,在助焊剂浸润区要求助焊剂在完成对焊件金属表面(焊盘和元件焊端)氧化层清洗的前提下,还要保持足够的活性,使助焊剂对熔融的焊料产生去氧化、降低液态焊料的粘度和表面张力、增加流动性、提高浸润性,使钎料熔化时就能迅速铺展开。因此要求助焊剂的活性温度范围覆盖整个钎焊温度。其次是助焊剂与钎料的流动、铺展进程要协调。使钎料的熔化与助焊剂的活性高潮保持同步。一般要求助焊剂的熔化(活性化)温度在焊料合金熔点前5~6s。
•回流区(或称为液相时间、熔点以上的时间)
从183℃再到183℃是回流区,回流区是焊料流动的液相区,因此也称液相区。有铅焊接的工艺窗口比较宽,一般为50~80s。有一些简单的组装板,40s就可以。
此区域是焊膏从熔化到凝固形成焊点的焊接区。回流区时间过短,可能会造成焊接不充分;时间过长,会形成过多的金属间化合物,还会使金属高温再氧化,影响焊点可靠性。
•峰值温度和时间
峰值区是扩散、溶解、冶金结合形成良好焊点的关键区域。如果峰值温度太低,液态焊料的黏度和表面张力太大,金属分子间扩散的动能很小,焊料刚刚熔化时,扩散速度非常慢,会使焊接不充分,很难在几秒钟内形成焊点。理论峰值温度一般设定在比合金熔点高15.7~71℃之间。经多年的实践证明,Sn-Pb合金在液相线之上30~40℃左右为最佳焊接温度, 63Sn-37Pb焊膏的熔点为183℃,有铅焊接时峰值温度为210~230℃左右,大约需要7~15s。
采用有铅焊料焊接有铅和无铅元器件时,由于无铅元件的焊端镀层和焊球的熔点高于锡铅焊料的熔点,因此,需要在原来有铅焊接的基础上适当提高温度,一般提高15~20℃。设置峰值温度和液相时间还要考虑IMC的厚度,峰值温度越高,IMC生长速度越快;液相时间越长,IMC越多。为了预防损坏有铅元件和PCB基板,还要缓慢升温、充分预热,尽量采用低峰值温度曲线。一般密度的组装板可以参考以下设置方案。
在PCBA上没有无铅PBGA时:一般控制在225~235℃,7~15s;
在PCBA上有无铅PBGA时:一般控制在230~245℃,7~15s
在PCBA上有CBGA和CCGA时:一般控制在250~260,7~15s℃
焊接热是温度和时间的函数。温度高,时间可以短一些;温度低,时间应长一些。
•冷却区
从峰值温度至炉子出口温度称为冷却区。在此区域焊料冷却、凝固,它是形成焊点的关键区域。冷却速率对焊点的质量有很大影响。对于焊点而言,要求快速冷却,快速冷却的结晶颗粒最小、焊点结构致密、强度高;但降温速度过快也会使焊点应力过大,过快降温会损坏陶瓷体(电阻、电容)、铁氧体(电感器)、玻璃体(圆柱形二极管)元件。综合考虑,冷却速率一般控制在-2~-4℃/s。
由于不同的再流焊炉,其出口的温度相差很大,因此不同炉子计算的斜率相差也很大。图12是用63Sn-37Pb焊料焊接有铅和无铅元器件混装再流焊冷却速率控制示意图。从理论上分析,冷却斜率分为三个阶段比较合理。第一阶段从峰值温度至固相线(63Sn-37Pb焊膏为183℃,SAC305为217℃),这一阶段是形成焊点的关键区域,快速冷却能够使焊点迅速凝固,结晶颗粒小,结构致密;时间过长,金属间化合物会迅速增加。第二阶段从固相线至100℃,这一阶段,尤其在凝固点附近快速冷却有利于减小偏析现象,此阶段时间过长也会对金属间化合物厚度的增加有一定影响。第三阶段从100℃至炉子出口,目前大多数再流焊炉出口温度在40~60℃之间。总之,要求有一个受控的冷却过程。
图12 用63Sn-37Pb焊料焊接有铅和无铅元器件混装再流焊冷却速率控制示意图
② 尽量采用低峰值温度曲线
所谓低峰值温度曲线,就是首先通过缓慢升温和充分预热,降低PCB表面温差Δt;在回流区,大元件和大热容量位置一般都滞后小元件到达峰值温度。图13是低峰值温度(230~240℃)曲线示意图。图中,实线为小元件的温度曲线,虚线为大元件的温度曲线。当小元件到达峰值温度时保持低峰值温度、较宽峰值时间,让小元件等候大元件;等大元件也到达峰值温度并保持几秒钟,然后再降温。通过这种措施可预防损坏元器件。
低峰值温度(230~240℃)接近传统有铅焊接的峰值温度,因此损坏器件风险小,能耗少;但对PCB的布局、热设计、回流焊接工艺曲线的调整、工艺控制,以及对设备横向温度均匀性等要求比较高。低峰值温度曲线不是对所有产品都适用,实际生产中一定要根据PCB、元器件、焊膏等的具体情况设置温度曲线,复杂的板可能需要250~260℃。
图13 低峰值温度(230~240℃)曲线示意图
一块PCB上有几百、几千个元件,有几千至上万个焊点,其中只要有一个元件、一个焊点失效,这台机器就会发生故障或不能正常工作。为了保证每个焊点的连接可靠性,必须减小PCB表面的Δt,满足微小的混装工艺窗口。除了要正确设置温度曲线外,还需要从多方面配合,例如,要求从PCB设计时就要考虑热分布均匀等措施;设备方面,一般要求再流焊炉横向温差<±2℃等等。总之,只有全面控制才能保证稳定的质量。
③ 设备控制不等于过程控制
再流焊炉中装有温度(PT)传感器来控制炉温。例如将加热器的温度设置为230℃,当PT传感器探测出温度高于或低于设置温度时,就会通过PID闭环控制加热速度和时间。然而,这并不是实际的工艺控制信息。由于PCB的质量、层数、组装密度、进入炉内的PCB数量、传送速度、气流等的不同,进入炉子的PCB的温度曲线也是不同的,因此,再流焊工序的过程控制不只是监控机器的控制数据,而是对制造的每块PCB的温度曲线进行监控。否则它就只是机器控制,算不上真正的工艺过程控制。
④ 再流焊炉的参数设置必须以工艺控制为中心
根据再流焊技术规范对再流焊炉进行参数设置(包括各温区的温度设置、传送速度、风量等),但这些一般的参数设置对于许多产品的焊接要求是远远不够的。例如较复杂的印制板要使最大和最小元件都能达到0.5~4μm界面合金层厚度,当PCB进炉的数量发生变化时、当环境温度或排风量发生变化时、当电源电压和风机转速发生波动时,都可能不同程度的影响每个焊点的实际温度。因此如果产生的实时温度曲线接接近于上限值或下限值,这种工艺过程就不稳定。由于工艺过程是动态的,即使出现很小的工艺偏移,也可能会发生不符合技术规范的现象。
由此可见,再流焊炉的参数设置必须以工艺控制为中心,避开技术规范极限值。这种经过优化的设备设置可容纳更多的变量,同时不会产生不符合技术规范的问题。
⑤ 必须正确测试再流焊实时温度曲线,确保测试数据的精确性。
需要考虑以下因素:
•热电偶本身必须是有效的:定期检查和校验
•必须正确选择测试点:能如实反映PCB高、中、低温度
•热电偶接点正确的固定方法并必须牢固
•要考虑元器件封装形式和热传导方式
•还要考虑热电偶的精度、测温的延迟现象等因素
⑥ 通过监控工艺变量,预防缺陷的产生
•当工艺开始偏移失控时,工程技术人员可以根据实时数据、进行分析、判断(是热电偶本身的问题、接点固定的问题、还是炉子温度失控、传送速度、风量发生变化……),然后根据判断结果进行处理。
•通过快速调整工艺的最佳过程控制,预防缺陷的产生。
•目前能够连续监控再流焊炉温度曲线的软件和设备也越来越流行。(例如KIC公司推出的温度监控系统——包括硬件和软件)
在SMT工艺中,有的组装板可能需要经过2~3次再流焊,有的组装板需要经过再流焊、波峰焊和烙铁焊多次或多种焊接方法,多次焊接会增加金属间化合物的生成,使金属间化合物层变厚,因此还要注意双面回流焊和尽量避免返修作业。例如双面回流焊时更要注意尽量不要设置过高的温度和时间;通过工艺控制尽量使SMT实现:通过印刷焊膏、贴装元器件、最后从再流焊炉出来的表面组装板的合格率达到或接近达到100%,也就是说要求实现零(无)缺陷或接近零缺陷的再流焊接质量,同时还要求所有的焊点达到一定的机械强度。只有这样的产品才能实现高质量、高可靠。
⑸ 有铅/无铅混装波峰焊工艺控制
波峰焊也要按照焊接理论、温度曲线、正确操作。
波峰焊工艺中采用有铅焊料焊接有铅和无铅元器件时,锡波的温度在240~250℃左右,由于没有BGA器件,因此,一般不需要提高温度,但是也要注意对Sn-Bi元件的管理。
建议:
① 很多缺陷与PCB设计有关,必须考虑DFM;
② 很多缺陷与PCB、元件质量有关,应选择合格的供应商,受控的物流、存储条件;
③ 很多缺陷源于助焊剂活性不够。好的助焊剂能够经受住高温,防止桥接,改善通孔的透过率;
④ 波峰焊的焊料温度尽可能设低,防止元件过热,材料损坏,尤其要控制混装工艺中二次回流;
⑤ 低的焊料温度能减轻焊锡氧化、减少锡渣,减轻熔融焊料对焊料槽及叶轮的侵蚀作用,限制FeSn2晶体的生成;
⑥ 优秀的工艺控制可以降低缺陷水平。工艺参数的综合调,必须控制温度曲线;
⑦ 注意锡炉中焊料的维护,加强设备的日常维护。
⑹ 手工焊接工艺控制
手工焊接也要了解焊接过程与焊接机理,按照焊接理论、温度曲线、正确操作。
•正确选择、使用电烙铁
•正确选择、使用焊锡丝、助焊剂
•混装焊接理想的焊接温度和时间( 63Sn/37Pb :230~245℃ /2~3s)
•温度越高、时间越长、金属间化合物越厚,焊点发脆
•掌握手工焊接的正确方法:焊接五步法
•避免:手工焊接中的7种错误操作
总之,有铅和无铅混用时,可能会发生材料之间、工艺之间、设计之间不相容等问题。因此,要求高可靠产品从产品设计开始就要考虑到混装的可靠性。选择最优秀的组装方式及工艺流程;选择合格的元器件、PCB基板材料、焊盘镀层、焊接材料、助焊剂;严格管理,特别是物料管理、工艺管理;对印刷、贴片、再流焊、波峰焊、手工焊、返修、清洗、检测等制造过程中所有工序进行全过程控制。按照焊接理论和正确的工艺方法把工艺做得更细致一些。这样才能比较有效地控制高可靠产品有铅和无铅混装工艺的质量。
如需看完整的技术文章:请订阅印刷版《SMT工艺与设备》杂志/电话:0755-25856945
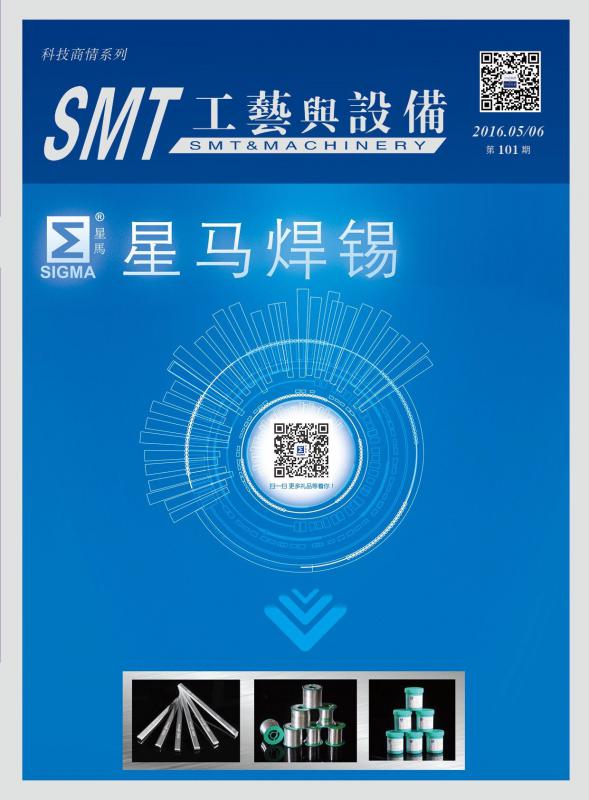
摘要:目前我国军工电子产品普遍存在有铅和无铅元器件混装焊接的现象,有铅和无铅混用时,可能会发生材料之间、工艺之间、设计之间不相容等问题,影响电子产品的可靠性。军工产品可靠性是第一位,既要保证焊点质量,又要保证不损坏元器件和印制板。本文通过对有铅和无铅混装焊接可能发生的不相容问题分析,对高可靠产品有铅和无铅混装工艺的质量控制方案提出一些建议。文章中的观点供参考并与同行共同讨论。
关键词:有铅焊料、有铅焊接、无铅焊料、无铅焊接、有铅元器件、无铅元器件、有铅和无铅混装、物料管理、可靠性、材料相容性、工艺相容性、设计相容性。
虽然电子产品无铅化在国际上已经有近20年的经验,国内也推行近10年了,目前在消费类、通信类等领域已经比较普遍地应用了无铅技术,总体来看也没有发生太大的可靠性问题。但是由于无铅焊点蠕变大,无铅焊料是“高锡”焊料。高锡带来的是高温、表面张力大、黏度大、浸润性差、工艺窗口小等问题,高温又会带来工艺上的难度,可能会导致的元件和电路板降级甚至损坏。另外,焊接温度越高金属间化合物生长速度越快,界面微孔、空洞多,金属间化合物是脆性的,无铅焊点比Sn-Pb焊点更硬也传递了更大的应力,这些问题都会影响无铅产品的长期可靠性。到目前为止,世界各国研究机构对无铅焊接可靠性等方面还没有统一的认识,无铅产品的长期可靠性在业内还存在争议,并确实存在不可靠因素,这也是国际上对军事、航空航天、医疗等高可靠要求领域的电子产品获得豁免的主要原因之一。由于汽车产品涉及人身安全,欧盟在2010年2月23日颁布了对ELV(End-of-Life Vehicle欧盟报废车辆指令)附件二的更新,新的ELV附件二规定汽车产品的含铅焊锡禁用期限被推迟1~5年(更新的主要内容:电子、电气元器件焊接到电路板上所使用的含铅焊锡,可延期到2016年1月1日;电解电容/铝电容引脚上的铅/锡,可延期到2013年1月1日;85%及以上的铅合金高温焊锡,可延期到2015年1月1日)。从期限被推迟可以看出高可靠产品无铅化的发展和替代锡铅的困难。虽然国际上高可靠产品获得豁免,而目前我国没有豁免政策,那么我们军工等高可靠领域怎么解决?这是近年来业界十分关心的问题。
从理论上来讲,就焊点来说,焊料、元器件焊端、PCB表面镀层全部是锡铅,或全部是无铅的相容性是最好的。目前,如果采用无铅焊接,可以买到所有的无铅元件。对于大多数民用、通信等领域,由于使用环境应力小、不恶劣,应用无铅焊接是没有问题的。对于军工等高可靠领域,其长期可靠性存在不确定因素,可能会有风险的。因此,建议军工等高可靠领域暂时还是采用有铅焊接相对比较安全一些。
目前的问题是有铅工艺买不全有铅元件,有铅工艺遇到85%甚至90%以上无铅元件,因此,我国军工电子产品普遍存在有铅和无铅元器件混装焊接的现象——目前大多采用有铅焊料焊接有铅和无铅元器件。本文对有铅和无铅混装焊接可能发生的不相容问题进行了较详细的分析,并对高可靠产品有铅和无铅混装工艺的质量控制方案提出一些建议。
一、有铅和无铅混装焊接可能发生的不相容问题分析
军工产品可靠性是第一位,既要保证焊点质量,又要保证不损坏元器件和印制板。采用有铅焊料焊接有铅和无铅元器件。有铅和无铅混装焊接时有85%甚至90%以上无铅元件,无铅元件的焊端镀层大多是镀纯Sn的,容易形成Sn须;采用有铅焊料焊接有铅和无铅元器件时,有铅焊料焊接有铅元器件时材料和熔点温度都是相容的;有铅焊料焊接无铅元器件时,Sn-Pb焊料的熔点183℃,无铅元件焊端镀层Sn熔点为232℃,无铅BGA焊球Sn-Ag-Cu熔点217℃。由于无铅元件焊端镀层和焊球的熔点高于Sn-Pb焊料的熔点,因此,焊接时需要提高焊接温度,高温可能损坏有铅元器件和PCB基板,特别是对潮湿敏感元器件的影响不可忽视;另外,PCB和工艺设计时,基板材料、PCB焊盘涂镀层材料选择不当也会发生材料不相容等等问题。
如果设计、工艺、采购、管理不当就有可能会发生材料之间、工艺之间、设计之间不相容问题,影响电子产品的长期可靠性。
1、锡晶须问题
晶须(Whisker)是指从金属表面生长出的细丝状、针状形单晶体,它能在固体物质的表面生长,易发生在Sn、Zn、Cd、Ag等低熔点金属表面。通常发生在0.5~50μm、厚度很薄的金属沉积层表面。典型的晶须直径为1~10μm,长度为1~500μm。过长的锡晶须可能导致短路,引发电子产品可靠性问题,见图1。
图1 锡晶须增长会引发电子产品可靠性问题
由于镀Sn工艺简单、成本比较低,因此,目前无铅元件焊端和引脚表面采用镀纯Sn工艺比较多,但由于Sn表面容易氧化形成很薄、厚度不均匀的氧化层。镀Sn时在Cu表面会生成金属间化合物Cu6Sn5,Cu6Sn5的膨胀系数比较大,加电后或温度变化时Cu6Sn5对Sn镀层产生压力,在不均匀处会把Sn推出来,形成Sn须。在高温、潮湿和有负载震动等应力的环境里,Sn晶须的生长速度会加快,过长的晶须如发生在窄间距QFP等元件引脚上容易造成短路,晶须可能立即生长,也可能要经过几千小时的潜伏期后才开始生长出来。使长期电气可靠性存在隐患。
针对锡晶须问题,业界做了许多研究,目前已经有一些有效抑制Sn晶须生长的措施,主要有以下措施:
⑴ 镀层合金化
在Sn中添加Pb、Ag、Bi、Cu、Ni、Fe、Zn等金属元素可以有效抑制Sn晶须生长。目前大多采用Sn-Ni镀层,也有采用Sn-Ag-Cu、Sn-Ag和 Sn-Cu的。日本、韩国的某些无铅元件焊端还有采用Sn-Ag-Bi、Sn-Bi镀层。
⑵ 中间镀层
在镀Sn前先镀一层其它金属元素作为阻挡层,通常采用Ni。一般先镀Ni(>1μm)再镀Sn(1~3μm),中间形成金属间化合物Ni3Sn4,由于Ni3Sn4比较稳定,不容易对Sn镀层产生挤压。
⑶ 镀暗Sn(不要镀亮Sn,亮Sn 容易生长Sn须)
⑷ 增加镀Sn厚度至8~10μm
⑸ 热处理
•退火(在烘箱中烘150℃/2h或170℃/1h)
•熔化、回流
⑹ 采用“敷形涂覆”工艺(俗称“三防”工艺)来解决
2、Sn-Pb焊料与无铅元件镀层材料不相容
从形成焊点的3个要素(焊料、元器件焊端、PCB表面镀层)来看,在传统的Sn-Pb焊接时,焊料是Sn-Pb,元器件焊端、PCB表面镀层大多也是Sn-Pb镀层,因此,焊接时焊料合金与被焊接金属之间的相容性非常好。
无铅元器件端表面镀层除了镀纯Sn外,还有镀Sn-Ag-Cu、Ni-Au、Ni-Pd-Au、Pd-Ag、Sn-Cu、Sn-Ag-Bi、Sn-Bi等合金层的。因此,在焊料与元件这一侧,可能会发生多种不同的界面反应;它们形成最佳金属间化合物的温度、时间等条件也有所差别;生成的金属间化合物的结构、厚度、强度、可靠性也有所不同了。在同一块组装板上,如果有一个元件、甚至只有一个焊点不相容,都可能造成整个电路的故障。下面举两个例子。
⑴ Sn-Pb焊料与Sn-Bi镀层不相容
焊料中的Pb与Sn-Bi镀层中的Bi在引脚或焊端界面形成Sn-Pb-Bi(熔点93℃)的三元共晶低熔点层、焊接后在焊点与焊端交界处会加剧分层Lift-off(如图2所示),使焊点浮起(焊缝起翘),严重时甚至会将PCB焊盘一起剥离开,导致焊接强度劣化。
图2 焊缝起翘现象(Lift-off)
⑵ Pd-Ag和Pd-Au端头镀层的元件回流焊时,由于浸析现象,容易在高温下过早溶解在焊料中,或者出现气泡,产生空洞,导致焊点接触不良。
3、高温可能损坏元器件封装体及内部连接、损坏PCB基材
传统的Sn-Pb焊料焊接有铅元器件时,其焊接温度一般不超过240℃,恰好在有铅元器件和PCB基材能够耐受的温度范围内。但是,有铅和无铅混装焊接时有大量的无铅元器件,无铅元件的焊端镀层和焊球的熔点高于Sn-Pb焊料的熔点,为了保证焊料与元件之间的连接强度,必须提高焊接温度,因此,采用有铅焊料焊接有铅和无铅元器件时,也存在高温的问题。高温可能损坏元器件和PCB基板。
例如,陶瓷电阻器和特殊的电容器对温度曲线的斜率(温度的变化速率)非常敏感,由于陶瓷体与PCB的热膨胀系数(CTE)相差较大(陶瓷为3~5ppm/℃,PCB为18ppm/℃左右),在焊点冷却凝固时容易造成元件体和焊点裂纹。元件开裂现象与CTE的差异、温度、元件的尺寸大小成正比。0201、0402、0603小元件一般很少开裂,而1206以上的大元件发生开裂失效的机会较多。又如,铝电解电容对温度极其敏感。有些钽电容只能承受183℃以上不能超过60s,240℃不能超过10s;一些小型表面贴装变压器的骨架不耐高温,要求220℃不能超过10s;有的有铅器件230℃不能超过10s;一些热敏元件如聚合物开关(PWS)在再流焊后阻值会发生变化,在温度降低后仍不能恢复。因此,需要注意对元器件的选择,避免高温对元器件损伤导致失效。图3 是高温损坏元件和PCB基板的例子。
(a)元件开裂 (b)连接器件损伤 (c)基板内部树脂损伤
图3 高温损坏元件和PCB基板
4、高温对湿度敏感器件(MSD)的不利影响
湿度敏感器件(MSD)主要指非气密性(Non-Hermetic)器件。包括:
塑料封装;
其他透水性聚合物封装(环氧、有机硅树脂等);
一般IC、芯片、电解电容、LED等。
采用有铅焊料焊接有铅和无铅元器件时,需要提高焊接温度,也存在高温问题。因此,还必须高度重视器件的潮湿敏感度问题。吸潮的器件在再流焊过程中由于水蒸气膨胀,使水蒸气压随温度升高而上升,对已经受潮的器件都会造成损坏的威胁。连接器和其他塑料封装元器件(如PBGA、QFP等)在高温时失效明显增加,主要是分层、爆米花、变形、开裂等。
(a)塑封器件封装开裂失效 (b)器件内部封装失效 (c)PBGA器件基板起泡
图4 受潮的湿度敏感器件受高温损坏
IPC与JEDEC共同制定的MSD潮湿敏感等级标准J-STD-033A是按照有铅元件220℃的焊接温度制订的,根据经验粗略统计,焊接温度每提高10℃,湿度敏感器件(MSD)的湿度敏感等级(MSL)提升1级,可靠性随之下降1级。如果Sn-Pb器件定级为MSL3,有铅焊料焊接有铅和无铅元器件时至少提高10~15℃,湿度敏感等级将提升到MSL4~MSL5。因此,再流焊工艺中要特别注意对湿度敏感器件(MSD)的管理,解决措施是对湿度敏感元器件(MSD)按照要求进行管理、存储和使用,尽量降低峰值温度,对已经受潮的潮湿敏感元器件进行
去潮烘烤处理。图4 是受潮的湿度敏感器件受高温损坏的例子。
5、PCB焊盘涂镀层ENIG(Ni/Au)的金脆和黑焊盘问题
ENIG(Ni/Au)俗称水金板,是化学镀Ni/闪镀金Au工艺。Ni层>3µm(一般5~7µm),Au层一般0.05~0.15µm,ENIG(Ni/Au)镀层表面平整、耐磨、接触电阻小、抗氧化,适用于高密度SMT板的双面再流焊工艺,是军工和高可靠产品PCB常选用的焊盘表面镀层。薄Au层在焊接时迅速熔于焊料中,露出清洁新鲜的Ni与熔融焊料中的Sn形成Ni3Sn4,使焊点更牢固。少量Au熔于锡中不会引起焊点变脆,Au层只起保护Ni层不被氧化的作用。图5是Sn系焊料与Ni/Au(ENIG)焊接后钎缝组织的扫描电子显微镜(SEM)照片。从图中可以看出,在Ni焊盘这一侧,Ni与焊料之间的金属间化合物主要是Ni3Sn4,在焊料一侧主要是AuSn4。Ni-Sn化合物比较稳定,Ni-Sn界面反应层与Sn-Cu反应层相比,反应速度比较慢一些,金属间化合物的厚度也相对薄得多,因此Ni-Sn合金的连接强度较好;但是Au能与焊料中的Sn形成Au-Sn间共价化合物AuSn4、AuSn2、AuSn(主要是AuSn4)。AuSn4不是我们需要的结合层。在焊点中金的含量超过3%会使焊点变脆,过多的Au原子替代Ni原子,因为太多的Au溶解到焊点里,无论与Sn-Pb还是与Sn-Ag-Cu焊接,都将引起“金脆”。所以一定要限定Au层厚度,通常用于焊接的Au层厚度≤1µm(钎焊时控制在0.05~0.15µm)。
图5 Sn系焊料与Ni/Au(ENIG)的钎缝组织
另外印制板加工时,如果ENIG(Ni/Au)的工艺参数控制不好,Ni被酸腐蚀或氧化,会造成“黑焊盘”现象。
关于ENIG 的“黑焊盘”(Black Pads in ENIG Finishes)问题说明如下。
图6是“黑焊盘”现象。黑焊盘是PCB制造厂的问题,有铅焊接也存在这个问题。黑焊盘处用手指一推,元件就会掉下来。
图6 “黑焊盘”现象
⑴ “黑焊盘”(Black Pads in ENIG Finishes)现象的产生原因
① 金镀层结构不够致密,表面存在针孔和裂缝,空气中的水汽容易进入,造成镍镀层氧化。
② 镍镀层磷含量偏高或偏低,导致镀层耐酸腐蚀性能差,易发生腐蚀变色,出现“黑焊盘”现象,使镀层可焊性变差。一般建议P 含量控制在7~9%,pH值为3~4较好。
③ 镀镍后没有将酸性镀液清洗干净,长时间 Ni被酸腐蚀。
④ 作为可焊性保护性涂覆层的Au镀层在焊接时会完全溶蚀到焊料中,而被氧化或腐蚀的Ni镀层由于可焊性差不能与焊料形成良好的金属间合金层,最终导致虚焊或焊点强度不足,使元件从PCB上脱落。
⑵ 关于富磷现象的解释
① 在化学镀Ni-P(镍-磷)的情况下,Ni向Sn一侧扩散,在焊料一侧形成较厚的Ni3Sn4(见图7左),造成Ni-P合金中Ni欠缺、P剩余,因此可以理解为形成了富P的Ni层(见图7右)。
② Ni3Sn4和富P的Ni层界面附近容易形成空洞(见图7右),空洞会降低界面的连接强度。
因此,高可靠产品选择ENIG(Ni/Au)板时,对PCB制造厂要提出质量控制的要求,
图7 Ni镀层与Sn合金界面的模型
6、有铅焊料与无铅PBGA、CSP混用必须提高焊接温度
有铅焊料与无铅PBGA、CSP混用时,如果采用有铅焊料的温度曲线,焊点连接可靠性是最差的。这是由于有铅焊料与无铅焊球的熔点不相同,有铅焊料熔点低先熔,而无铅焊球不能完全熔化,容易造成PBGA、CSP一侧焊点失效的缘故。
图8是有铅焊料与无铅焊球混用示意图。从图中可以看出,无铅PBGA、CSP的焊球一般是Sn-Ag-Cu合金,熔点高(217℃),Sn-37Pb焊料的熔点低(183℃),如果采用Sn-37Pb焊料的温度曲线,一般峰值温度在210~230℃。假设峰值温度为220℃,再流焊时,当温度上升到183℃时印刷在焊盘上的Sn-37Pb焊膏开始熔化,此时无铅PBGA的Sn-Ag-Cu焊球还没有熔化;当温度上升到220℃时,按照有铅工艺就要开始降温、结束焊接了,此时无铅焊球刚刚熔化。虽然Sn-Ag-Cu合金标称的熔点为217℃,但实际上Sn-Ag-Cu合金并不是真正的共晶合金,固相线与液相线的温度范围是216~220℃,因此,有铅工艺冷却凝固结束焊接的温度恰好是无铅Sn-Ag-Cu焊球刚刚熔化之时,并处于固、液相共存的浆糊状态。焊球熔化时由于器件重力的作用开始下沉,在器件下沉过程中稍有震动或PCB微量变形,便使PBGA、CSP元件一侧原来的焊接界面结构遭破坏,又不能形成新的界面金属间合金层,最终造成PBGA、CSP一侧焊点失效,如图9所示。因此有铅焊料与无铅焊球混用时,采用有铅焊接工艺的质量最差。解决上述问题的措施有两条。
⑴ 通过提高焊接温度的方法解决
必须提高焊接温度到235℃左右,使器件一侧的焊球实现二次回流,这样可以使器件一侧的焊球合金充分熔化,在焊球与器件的焊盘之间生成新的金属间化合物,形成良好的电气与机械连接。
⑵ 还要注意其他有铅元件能否承受高温
图8 有铅焊料与无铅焊球混用示意图 图9 PBGA、CSP在元件一侧的界面失效
7、电气可靠性
通常同一块PCB要经过回流焊、波峰焊、返修等工艺,很可能形成不同的残留物,在潮湿环境和一定电压下,可能会与导电体之间发生电化学反应,引起表面绝缘电阻(SIR)的下降。如果有电迁移和枝状结晶生长出现,将发生导线间的短路,造成电迁移(俗称“漏电”)的风险。图10是电迁移造成的树枝状结晶的例子。
为了保证电气可靠性,需要对不同免清洗助焊剂的性能进行评估,同一块PCB要尽量采用相同的助焊剂,或进行焊后清洗处理。
图10 电迁移造成的树枝状结晶
二、高可靠产品有铅和无铅混装工艺质量控制方案的建议
根据以上分析、讨论,可见:采用有铅焊料焊接有铅和无铅元器件工艺,如果设计、工艺、采购、管理不当就有可能会发生材料之间、工艺之间、设计之间等不相容问题,影响高可靠电子产品的长期可靠性。主要有锡晶须问题、Sn-Pb焊料与无铅元件镀层材料不相容、高温可能损坏元器件封装体及内部连接、高温可能损伤PCB基材、高温对湿度敏感器件(MSD)的不利影响、PCB焊盘涂镀层ENIG(Ni/Au)的金脆和黑焊盘问题、有铅焊料与无铅PBGA、CSP混用必须提高焊接温度、电气可靠性等等。另外,BGA器件有铅无铅混合球的长期可靠性问题也被提出了,目前还没有研究结果。
从以上的不可靠因素还可以看出,例如锡晶须、器件和PCB基材的内部损伤、金脆和黑焊盘、电气可靠性等都是隐蔽的缺陷。隐蔽的缺陷不容易被发现,因此往往不被重视。它们的可靠性都是随着时间的推移,在使用过程中由于受到机械震动、跌落或电路板被弯曲,受到环境温度、工作温度的循环热应力等因素的影响逐渐削弱的。这些隐蔽的缺陷增加了高可靠电子产品长期可靠性的不确定性。
因此,我们必须从产品设计开始就考虑到材料、工艺、设计之间的相容性;充分考虑散热问题;仔细地选择PCB板材、焊盘表面镀层、元件、焊膏及助焊剂等;比有铅焊接时更加细致地进行工艺优化和工艺控制;更加严格细致地进行物料管理。
下面对军工等高可靠电子产品,有铅和无铅混装工艺质量控制提出如下建议,供参考并与同行共同讨论。
1、暂时不建议采用无铅工艺,建议采用有铅焊料焊接有铅和无铅元器件工艺
如果决定实施无铅工艺,建议选择Sn-3.5 Ag二元共晶合金。其主要理由是Sn-3.5 Ag合金已在某些高可靠电子领域应用了很长时间,已经完成大量测试,并且已被高可靠领域广泛接受。同时,一定要做可靠性认证。
2、严格物料管理
虽然目前的混装工艺采用有铅焊料焊接有铅和无铅元器件,但是遇到含Bi无铅元器件时需要采用无铅焊料焊接,生产线还可能存在两种焊料,因此,元件和材料管理很重要。
⑴ 物料管理的一般要求
① 元器件采购技术要求。对采购部门进行ROHS培训,加强对上游供应商的管理。
② 备料。首先要注意元器件的焊端材料是否无铅,如果是无铅元器件,一定要弄清楚是什么镀层材料,特别是BGA\CSP和新型封装的器件,如QFN等。BOM表上必须标注的内容包括焊端表面镀层材料、最高耐受温度和时间、潮敏度等级。
③ 标识和标签。应给无铅元器件做无铅标识和标签。
④ 规定无铅元器件编号方式。
⑤ 识别。对生产线操作人员进行培训,提高对无铅标识、标签的识别能力。并自觉遵守无铅管理制度
⑥ 材料管理自动化。生产过程中可以用手工扫描条形码标签,也可以通过贴片机上的RFID智能供料器识别,实现材料管理自动化。
⑦ 生产线设置验证。为了防止贴片机上装错元件,从而造成不必要的损失,应使生产线的设置通过手工、半自动或闭环验证。
⑧ 可追溯性与材料清单。可追溯性要求对每一块组装板编一个独一无二的序号,然后将这块组装板上所有的元器件及组装工艺的信息记录在案,一旦出现问题,很容易追溯到问题的根源。这种管理是当前最先进的方法,但需要很大的投资。
⑨ 无铅元器件、工艺材料的储存。 在储存方面,企业可以考虑设立单独的无铅工艺材料、无铅元器件、用于无铅的模板和工具的仓库,或从现有的仓库划出相当的空间用于无铅物料、工具等物品的储存。
⑩ 无铅的专用工具。必须具备无铅专用模板、烙铁或焊台、镊子、刷子等工具,并做标识。
设立无铅手工焊接的专用工位。
⑿ 加强静电防护与管理措施
⒀ 对湿度敏感器件(MSD)采取正确的控制措施
⑵ 设计人员在BOM表上必须标注的内容
•元器件的内引线材料、焊端表面镀层材料;
•最高耐温及最高温度下的耐受时间;
•最大升温和降温斜率;
•潮敏度等级。
⑶ 工艺人员根据设计文件进行工艺控制和设计温度曲线
•例如对潮敏元件、含Bi元件的控制等
⑷ 操作人员要按照正确的工艺方法实施
3、用有铅焊料焊接有铅和无铅元器件的原则
⑴ 焊接材料的选择
① 焊料合金:选择Sn-37Pb共晶合金或62Sn-36Pb-2Ag
合金成分是决定焊料熔点及焊点质量的关键参数,应尽量选择共晶或近共晶合金。选择共晶合金具有以下好处:
•共晶合金的熔点最低,焊接温度也最低,焊接时不会损坏元件和印制板;
•所谓共晶焊料就是由固相变液相或由液相变固相均在同一温度下进行,降温时当温度降到共晶点时,液态焊料一下子全部变成固相状态,因此焊点凝固时形成的结晶颗粒最小,结构最致密,有利于提高焊点强度;
•共晶合金在冷却凝固时只要降到共晶点温度,就会立即从液相变成固相,因此共晶合金在凝固过程中没有塑性范围,有利于焊接工艺的控制。合金凝固温度范围(塑性范围)对焊接的工艺性和焊点质量影响极大。塑性范围大的合金,在合金凝固、形成焊点时需要较长时间,如果在合金凝固期间PCB和元器件有任何震动(包括PCB变形),都会造成“焊点扰动”,有可能会发生焊点开裂,使电子设备过早损坏。
② 焊膏的选择
•免清洗产品选择免清洗焊膏
•需要清洗和需要做三防工艺的产品应选择溶剂清洗焊膏,或水清洗焊膏
③ 助焊剂的选择
助焊剂在焊接中起着十分重要的作用。它能够去除被焊金属表面的氧化物;防止焊接时焊料和焊接表面的再氧化;降低焊料的表面张力,增强润湿性;有利于热量传递到焊接区。助焊剂的种类非常多,据统计大约有几百种规格。常用助焊剂有4类:松香型助焊剂、水溶性助焊剂、低固含量的免清洗助焊剂、无VOC助焊剂。
助焊剂的性能直接影响焊接质量,如果选择不当,不仅起不到助焊作用,反而会造成机械强度降低、电化学腐蚀、电迁移等可靠性问题。因此,正确选择助焊剂十分重要。助焊剂通常与焊料匹配使用,要根据焊料合金,根据不同的工艺方法,同时还要根据被焊的元件引脚、PCB焊盘的涂镀层材料、金属表面氧化程度,以及产品对清洁度和电性能的具体要求进行选择。
•一般情况下,军用及生命保障类如卫星、飞机仪表、潜艇通信、保障生命的医疗装置、微弱信号测试仪器等电子产品必须采用清洗型的助焊剂。
•通信类、工业设备类、办公设备类、计算机等类型的电子产品可采用免清洗或清洗型的助焊剂。
•一般家用电器类电子产品均可采用免清洗型助焊剂,或采用RMA(中等活性)松香型助焊剂,可不清洗。
•手工焊接和返修时一定要选择与再流焊、波峰焊时相同的助焊剂。
•水溶性焊剂的可焊性非常好,常用于高可靠和金属表面氧化较严重的场合。但由于其残留物的腐蚀性很大,因此在使用过程中,需经常添加专用的稀释剂调节活性剂浓度,以确保良好的焊接效果。并要求焊后2小时内必须进行清洗。
⑵ 对PCB设计的要求
① PCB基板材料的选择
PCB基板材料主要根据电子产品的性能指标、使用环境、焊接温度来选择的。
•焊接温度240℃以下的产品,采用FR4环氧玻璃纤维基板;
•焊接温度240~250℃的产品,可选择高Tg(150~170℃)FR-4;
•高可靠及厚板,焊接温度250℃以上的产品,采用FR-5;
•使用环境温度较高或挠性电路板采用聚酰亚胺玻璃纤维基板;
•对于散热要求高的高可靠电路板采用金属基板;
•对于高频电路则需要采用聚四氟乙烯玻璃纤维基板。
② PCB焊盘涂镀层的选择
PCB焊盘涂镀层是根据焊料和工艺选择的,优先选择与传统有铅工艺相容的镀层材料。
(a)一般组装密度:选择Sn-Pb热风整平法(HASL),因为HASL与Sn-Pb焊料最相容。
(b)高组装密度:选择化学镀镍-金(ENIG)。化学镀Ni-Au是指PCB连接盘上化学镀Ni(厚度≥3μm)后再镀上一层0.05~0.15μm的薄金。在选择ENIG后,一定要保证ENIG的工艺质量。
(c)高可靠产品:可选择电镀镍金,Ni镀层厚度3~6µm ,Au层厚度0.05~0.15μm。
(d)特殊情况还可以选择Ni-Pd-Au镀层。Ni层厚度3~6µm ,Pa层厚度0.1~0.5µm ,金层厚度0.02~0.1µm。
③ 元器件的选择
•尽量选择有铅元件;
•对于那些镀Sn焊端的有引脚和无引脚无铅元件,因为Sn与Sn-Pb焊料焊接时是兼容的,至于镀Sn焊端的锡须问题,还可以通过对组装板的“敷形涂覆”工艺(俗称“三防”工艺)来解决,但是要特别警惕混入镀Sn-Bi元件。
•如果有Sn-Bi元件,可以采用Sn-Ag-Cu焊料手工焊接(必须设立无铅手工焊接的专用工位,专用工具,并做标识)。
•对于无铅PBGA、CSP,一般情况可以通过适当提高焊接温度解决,使器件一侧的焊球合金充分熔化,在焊球与器件的焊盘之间形成良好的电气与机械连接。
④ PCB焊盘设计
按照国际、国内行业、企业高可靠产品设计规范
⑶ 组装方式与工艺流程设计设计
首先要确定组装方式及工艺流程。组装方式与工艺流程设计合理与否,直接影响组装质量、生产效率和制造成本。
① 组装方式与工艺流程、焊接方式设计原则
•选择最简单、质量最优秀的工艺
•选择自动化程度最高、劳动强度最小的工艺
•工艺流程路线最短
•工艺材料的种类最少
•选择加工成本最低的工艺
② 工艺流程及焊接方式设计
主要根据印制板的组装密度和本单位SMT生产线设备条件。高可靠产品可作如下考虑。
•尽量采用再流焊方式,不采用或少采用波峰焊、手工焊工艺。因为再流焊工艺简单、质量优秀、自动化程度高、工艺流程路线短、工艺材料的种类少、加工成本低。
•当通孔元件的比例只占元件总数的10%~5%甚至以下时,可以考虑选择通孔元件再流焊工艺。通孔元件再流焊工艺与波峰焊工艺相比具有工艺简单、焊接质量好、成本低等优点。
•可以采用选择性波峰焊技术替代手工焊接。传统波峰焊工艺是PCB的焊接面(辅面)完全浸入液态焊料中,而在选择性波峰焊,仅有部分特定区域与焊锡波接触。选择性波峰焊技术比手工焊接的效率高、质量好。
•激光焊接也是最近几年国际上高可靠电子产品流行的焊接方法,激光焊接技术是非接触式焊接,不会伤害元件和印制板,温度控制精确,焊接质量好。
⑷ 再流焊工艺控制
① 运用焊接理论,正确设置和优化再流焊温度曲线
混装焊接时,升温区、预热区、助焊剂浸润区、峰值温度和液相时间等参数设置介于有铅(Sn-37Pb)和无铅(Sn-3.0Ag-0.5Cu)之间。
图11是用63Sn-37Pb焊料焊接有铅和无铅元器件混装再流焊温度曲线示意图。
110℃ 130℃ 155℃ 185℃ 240℃ 260℃ 90℃
PCB入口 出口
100℃ 130℃ 165℃ 195℃ 240℃ 260℃ 90℃
传送带速度:60cm/min
温度℃
焊接时间
峰值温度
230~245
183
150 1.2~3.5℃/s
2~4min
100
冷却区
<2℃/s 0.55~1℃/s -2~-4℃/s
升温区 预热区 回流区 时间min
60~90s 60~120s 20~50s 50~80s
助焊剂浸润区
(快速升温区)
图11 用63Sn-37Pb焊料焊接有铅和无铅元器件混装再流焊温度曲线示意图
下面结合图11介绍如何运用焊接理论,正确设置和优化混装再流焊温度曲线。
在实施再流焊过程控制之前,必须了解再流焊的焊接机理,确定明确的技术规范。
确定再流焊技术规范的依据:首先是焊膏供应商提供的温度曲线,因为焊膏中的合金成分决定了熔点,助焊剂的成分、性质决定了活化温度和活化温度范围;其次是元器件和PCB材料能承受的最高极限温度及其他要求;表面组装板搭载元器件的密度、元器件的大小以及有无CBGA、CCGA等特殊元器件;还要根据设备的具体情况,例如加热区长度、加热源材料、再流焊炉构造和热传导方式、排风量的大小、温度传感器的实际位置等因素来确定各温区的设置温度。有时环境温度对炉温也有影响,特别是加热温区短、炉体宽度窄的再流焊炉,在炉子进出口处要避免对流风。
再流焊技术规范一般包括以下内容:
•最高的升温速率
从室温到100℃为升温区,也称干燥区、预热1区。升温速度一般控制在<2℃/s,或160~170℃前的升温速度控制在1~2℃/s。
在升温区,随着温度升高,焊膏的黏度下降,焊膏塌落、覆盖焊盘,将焊盘、元器件引脚与氧气隔离;另外,焊膏中的溶剂、气体蒸发掉。溶剂的沸点一般在80℃左右,如果升温速度过快,容易使焊膏合金中的微粉(微小颗粒)随溶剂挥发而飞溅到PCB焊盘以外的地方,回流时造成微小焊锡珠;如果升温速度过慢,溶剂等气体挥发不干净,回流时也会造成飞溅。另外,有些潮湿敏感元件升温速率要求控制在0.5~1.5℃/s,一般不超过2℃/s,因此,需要控制升温区的升温速度。
•预热温度和时间
100~150(或170)℃为预热区,也称预热2区或保温区。预热区的时间约60~120s。
在预热区,PCB和元器件得到充分预热。缓慢升温、充分预热的作用是避免元器件及PCB突然进入回流区,由于受热太快而损坏元器件、造成PCB变形;充分预热的另一个作用是减小PCB各处及大小元器件的温差Δt,有利于降低回流时大小元器件的焊接温差。但是,如果预热温度太高、时间过长,容易使焊膏中的助焊剂提前被全部烧掉,造成焊料合金融化时助焊剂完全丧失活性,严重时会使合金粉末受高温再氧化,影响焊接质量。因此,预热温度不能超过助焊剂的活化温度(有铅焊膏中助焊剂的活化温度一般为174℃)。复杂的、大尺寸、厚的热容量大的多层板,组装密度高、元件尺寸和质量大的组装板,预热温度需要高一些、预热时间长一些,回流焊时吸热就少一些,有利于降低大小元件的Δt。
•助焊剂浸润区(活化)温度和时间
150(或174)~183℃为助焊剂浸润区,或称为快速升温区。理想的升温速度为1.2~3.5℃/s,最多控制在0.55~3.2℃/s,大约20~50s(有铅焊接时还可以接受)。
在助焊剂浸润区,焊膏中的助焊剂润湿焊盘、元件焊端,并清洗氧化层。我们知道,焊膏中助焊剂的主要成分是松脂(树脂)、活化剂、溶剂和少量其他添加剂。松脂的活化温度在174℃左右,恰好在Sn-37Pb合金熔点(183℃)之下。所谓“活化”就是发生分解反应,在活化温度下松香酸能够起到清洗氧化铜的作用。
正确控制助焊剂浸润区的温度和时间对提高焊点质量具有重要意义。因为钎焊焊接只能在清洁的金属表面进行。此阶段的作用是清理焊件的被焊界面,把界面的氧化膜及附着的污物清除干净。助焊剂浸润区的温度和时间是根据焊膏中助焊剂的活化温度来确定的。如果助焊剂浸润区的温度太低、时间太短,不能在合金熔化前充分清洗焊件表面的氧化层,就会造成合金熔化时由于反应太剧烈而产生焊液飞溅,形成锡珠、气孔;如果助焊剂浸润区的温度过高、时间过长,又会使助焊剂提前失效,影响液态焊料的浸润性,影响金属间合金层(或称为金属间化合物)的生成。
总之,在助焊剂浸润区要求助焊剂在完成对焊件金属表面(焊盘和元件焊端)氧化层清洗的前提下,还要保持足够的活性,使助焊剂对熔融的焊料产生去氧化、降低液态焊料的粘度和表面张力、增加流动性、提高浸润性,使钎料熔化时就能迅速铺展开。因此要求助焊剂的活性温度范围覆盖整个钎焊温度。其次是助焊剂与钎料的流动、铺展进程要协调。使钎料的熔化与助焊剂的活性高潮保持同步。一般要求助焊剂的熔化(活性化)温度在焊料合金熔点前5~6s。
•回流区(或称为液相时间、熔点以上的时间)
从183℃再到183℃是回流区,回流区是焊料流动的液相区,因此也称液相区。有铅焊接的工艺窗口比较宽,一般为50~80s。有一些简单的组装板,40s就可以。
此区域是焊膏从熔化到凝固形成焊点的焊接区。回流区时间过短,可能会造成焊接不充分;时间过长,会形成过多的金属间化合物,还会使金属高温再氧化,影响焊点可靠性。
•峰值温度和时间
峰值区是扩散、溶解、冶金结合形成良好焊点的关键区域。如果峰值温度太低,液态焊料的黏度和表面张力太大,金属分子间扩散的动能很小,焊料刚刚熔化时,扩散速度非常慢,会使焊接不充分,很难在几秒钟内形成焊点。理论峰值温度一般设定在比合金熔点高15.7~71℃之间。经多年的实践证明,Sn-Pb合金在液相线之上30~40℃左右为最佳焊接温度, 63Sn-37Pb焊膏的熔点为183℃,有铅焊接时峰值温度为210~230℃左右,大约需要7~15s。
采用有铅焊料焊接有铅和无铅元器件时,由于无铅元件的焊端镀层和焊球的熔点高于锡铅焊料的熔点,因此,需要在原来有铅焊接的基础上适当提高温度,一般提高15~20℃。设置峰值温度和液相时间还要考虑IMC的厚度,峰值温度越高,IMC生长速度越快;液相时间越长,IMC越多。为了预防损坏有铅元件和PCB基板,还要缓慢升温、充分预热,尽量采用低峰值温度曲线。一般密度的组装板可以参考以下设置方案。
在PCBA上没有无铅PBGA时:一般控制在225~235℃,7~15s;
在PCBA上有无铅PBGA时:一般控制在230~245℃,7~15s
在PCBA上有CBGA和CCGA时:一般控制在250~260,7~15s℃
焊接热是温度和时间的函数。温度高,时间可以短一些;温度低,时间应长一些。
•冷却区
从峰值温度至炉子出口温度称为冷却区。在此区域焊料冷却、凝固,它是形成焊点的关键区域。冷却速率对焊点的质量有很大影响。对于焊点而言,要求快速冷却,快速冷却的结晶颗粒最小、焊点结构致密、强度高;但降温速度过快也会使焊点应力过大,过快降温会损坏陶瓷体(电阻、电容)、铁氧体(电感器)、玻璃体(圆柱形二极管)元件。综合考虑,冷却速率一般控制在-2~-4℃/s。
由于不同的再流焊炉,其出口的温度相差很大,因此不同炉子计算的斜率相差也很大。图12是用63Sn-37Pb焊料焊接有铅和无铅元器件混装再流焊冷却速率控制示意图。从理论上分析,冷却斜率分为三个阶段比较合理。第一阶段从峰值温度至固相线(63Sn-37Pb焊膏为183℃,SAC305为217℃),这一阶段是形成焊点的关键区域,快速冷却能够使焊点迅速凝固,结晶颗粒小,结构致密;时间过长,金属间化合物会迅速增加。第二阶段从固相线至100℃,这一阶段,尤其在凝固点附近快速冷却有利于减小偏析现象,此阶段时间过长也会对金属间化合物厚度的增加有一定影响。第三阶段从100℃至炉子出口,目前大多数再流焊炉出口温度在40~60℃之间。总之,要求有一个受控的冷却过程。
图12 用63Sn-37Pb焊料焊接有铅和无铅元器件混装再流焊冷却速率控制示意图
② 尽量采用低峰值温度曲线
所谓低峰值温度曲线,就是首先通过缓慢升温和充分预热,降低PCB表面温差Δt;在回流区,大元件和大热容量位置一般都滞后小元件到达峰值温度。图13是低峰值温度(230~240℃)曲线示意图。图中,实线为小元件的温度曲线,虚线为大元件的温度曲线。当小元件到达峰值温度时保持低峰值温度、较宽峰值时间,让小元件等候大元件;等大元件也到达峰值温度并保持几秒钟,然后再降温。通过这种措施可预防损坏元器件。
低峰值温度(230~240℃)接近传统有铅焊接的峰值温度,因此损坏器件风险小,能耗少;但对PCB的布局、热设计、回流焊接工艺曲线的调整、工艺控制,以及对设备横向温度均匀性等要求比较高。低峰值温度曲线不是对所有产品都适用,实际生产中一定要根据PCB、元器件、焊膏等的具体情况设置温度曲线,复杂的板可能需要250~260℃。
图13 低峰值温度(230~240℃)曲线示意图
一块PCB上有几百、几千个元件,有几千至上万个焊点,其中只要有一个元件、一个焊点失效,这台机器就会发生故障或不能正常工作。为了保证每个焊点的连接可靠性,必须减小PCB表面的Δt,满足微小的混装工艺窗口。除了要正确设置温度曲线外,还需要从多方面配合,例如,要求从PCB设计时就要考虑热分布均匀等措施;设备方面,一般要求再流焊炉横向温差<±2℃等等。总之,只有全面控制才能保证稳定的质量。
③ 设备控制不等于过程控制
再流焊炉中装有温度(PT)传感器来控制炉温。例如将加热器的温度设置为230℃,当PT传感器探测出温度高于或低于设置温度时,就会通过PID闭环控制加热速度和时间。然而,这并不是实际的工艺控制信息。由于PCB的质量、层数、组装密度、进入炉内的PCB数量、传送速度、气流等的不同,进入炉子的PCB的温度曲线也是不同的,因此,再流焊工序的过程控制不只是监控机器的控制数据,而是对制造的每块PCB的温度曲线进行监控。否则它就只是机器控制,算不上真正的工艺过程控制。
④ 再流焊炉的参数设置必须以工艺控制为中心
根据再流焊技术规范对再流焊炉进行参数设置(包括各温区的温度设置、传送速度、风量等),但这些一般的参数设置对于许多产品的焊接要求是远远不够的。例如较复杂的印制板要使最大和最小元件都能达到0.5~4μm界面合金层厚度,当PCB进炉的数量发生变化时、当环境温度或排风量发生变化时、当电源电压和风机转速发生波动时,都可能不同程度的影响每个焊点的实际温度。因此如果产生的实时温度曲线接接近于上限值或下限值,这种工艺过程就不稳定。由于工艺过程是动态的,即使出现很小的工艺偏移,也可能会发生不符合技术规范的现象。
由此可见,再流焊炉的参数设置必须以工艺控制为中心,避开技术规范极限值。这种经过优化的设备设置可容纳更多的变量,同时不会产生不符合技术规范的问题。
⑤ 必须正确测试再流焊实时温度曲线,确保测试数据的精确性。
需要考虑以下因素:
•热电偶本身必须是有效的:定期检查和校验
•必须正确选择测试点:能如实反映PCB高、中、低温度
•热电偶接点正确的固定方法并必须牢固
•要考虑元器件封装形式和热传导方式
•还要考虑热电偶的精度、测温的延迟现象等因素
⑥ 通过监控工艺变量,预防缺陷的产生
•当工艺开始偏移失控时,工程技术人员可以根据实时数据、进行分析、判断(是热电偶本身的问题、接点固定的问题、还是炉子温度失控、传送速度、风量发生变化……),然后根据判断结果进行处理。
•通过快速调整工艺的最佳过程控制,预防缺陷的产生。
•目前能够连续监控再流焊炉温度曲线的软件和设备也越来越流行。(例如KIC公司推出的温度监控系统——包括硬件和软件)
在SMT工艺中,有的组装板可能需要经过2~3次再流焊,有的组装板需要经过再流焊、波峰焊和烙铁焊多次或多种焊接方法,多次焊接会增加金属间化合物的生成,使金属间化合物层变厚,因此还要注意双面回流焊和尽量避免返修作业。例如双面回流焊时更要注意尽量不要设置过高的温度和时间;通过工艺控制尽量使SMT实现:通过印刷焊膏、贴装元器件、最后从再流焊炉出来的表面组装板的合格率达到或接近达到100%,也就是说要求实现零(无)缺陷或接近零缺陷的再流焊接质量,同时还要求所有的焊点达到一定的机械强度。只有这样的产品才能实现高质量、高可靠。
⑸ 有铅/无铅混装波峰焊工艺控制
波峰焊也要按照焊接理论、温度曲线、正确操作。
波峰焊工艺中采用有铅焊料焊接有铅和无铅元器件时,锡波的温度在240~250℃左右,由于没有BGA器件,因此,一般不需要提高温度,但是也要注意对Sn-Bi元件的管理。
建议:
① 很多缺陷与PCB设计有关,必须考虑DFM;
② 很多缺陷与PCB、元件质量有关,应选择合格的供应商,受控的物流、存储条件;
③ 很多缺陷源于助焊剂活性不够。好的助焊剂能够经受住高温,防止桥接,改善通孔的透过率;
④ 波峰焊的焊料温度尽可能设低,防止元件过热,材料损坏,尤其要控制混装工艺中二次回流;
⑤ 低的焊料温度能减轻焊锡氧化、减少锡渣,减轻熔融焊料对焊料槽及叶轮的侵蚀作用,限制FeSn2晶体的生成;
⑥ 优秀的工艺控制可以降低缺陷水平。工艺参数的综合调,必须控制温度曲线;
⑦ 注意锡炉中焊料的维护,加强设备的日常维护。
⑹ 手工焊接工艺控制
手工焊接也要了解焊接过程与焊接机理,按照焊接理论、温度曲线、正确操作。
•正确选择、使用电烙铁
•正确选择、使用焊锡丝、助焊剂
•混装焊接理想的焊接温度和时间( 63Sn/37Pb :230~245℃ /2~3s)
•温度越高、时间越长、金属间化合物越厚,焊点发脆
•掌握手工焊接的正确方法:焊接五步法
•避免:手工焊接中的7种错误操作
总之,有铅和无铅混用时,可能会发生材料之间、工艺之间、设计之间不相容等问题。因此,要求高可靠产品从产品设计开始就要考虑到混装的可靠性。选择最优秀的组装方式及工艺流程;选择合格的元器件、PCB基板材料、焊盘镀层、焊接材料、助焊剂;严格管理,特别是物料管理、工艺管理;对印刷、贴片、再流焊、波峰焊、手工焊、返修、清洗、检测等制造过程中所有工序进行全过程控制。按照焊接理论和正确的工艺方法把工艺做得更细致一些。这样才能比较有效地控制高可靠产品有铅和无铅混装工艺的质量。
如需看完整的技术文章:请订阅印刷版《SMT工艺与设备》杂志/电话:0755-25856945
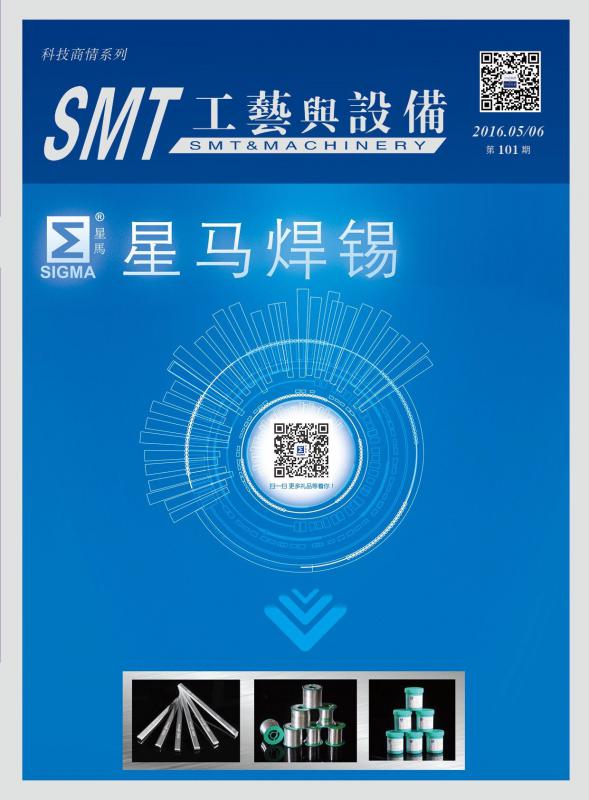
版权所有 ©深圳市亚中咨询有限公司
电话:0755-25856945 邮箱:pzl88smt@126.com 网址:www.smt668.com
地址:深圳市罗湖区怡正发大厦 SMT专业网版权所有(c) 2010 粤ICP备17073069号
本站部分图文来源网络,如有侵权问题请通知我们处理!
网站建设维护