视频专区
Current Location:HOME
- Author:
- Source:
- Date: 2016-01-28
- Views: 6526Times
摘 要:BGA(Ball Grid Array球栅阵列封装)应用已经进入了大规模实用化阶段,无论消费类电子、医疗安全产品还是航天军工电子,都有着广泛的应用,随之而来的是日益增加的BGA元件的返修种类和数量,本文针对BGA的特点,结合日常维修中的经验,浅谈一下BGA的返修。
关键词: PBGA,CBGA,温度曲线,助焊膏,植球,翘曲
1. BGA器件的分类和特点
说起BGA的返修,首先我们先了解一下这种器件的特点。BGA封装的I/O端子以圆形或柱状焊点按阵列形式分布在封装下面,焊点的加热熔化主要通过封装体与PCB的热传导。
BGA主要有PBGA,CBGA,CCGA和TBGA几大类,我们目前生产中比较常见的是PBGA和CBGA。
PBGA (plastic BGA)是塑料封装的BGA(见图1),也是目前使用较多的BGA,它使用63/37(有铅)或者305(无铅)成分的焊锡球,焊锡的熔化温度为183℃或者217℃。PBGA的优点是成本较低,容易加工,不过由于塑料封装,容易吸潮。
CBGA(ceramic BGA)是陶瓷封装的BGA(见图2),也有一定范围的应用,CBGA焊球的成分为90Pb/10Sn(它与PCB连接处的焊锡成分仍为63Sn/37Pb)。CBGA是在元件和印制板上采用不熔焊球(实际上是它的熔点大大高于回流焊的温度),焊球直径为0.889mm,高度保持不变。CBGA的焊锡球较PBGA不容易吸潮,且封装的更牢靠,CBGA芯片底部焊点直径要比PCB上的焊盘大,拆除CBGA芯片后,焊锡不会在PCB的焊盘上。
BGA与其他类型元件的区别就是焊点在元件本体的下部,不能够通过烙铁等常规工具进行拆卸焊接,而且拆卸焊接过程也不能够看到焊点的熔化和固化过程。这就决定了BGA维修的特殊性。下面我们就从上述应用最广泛的PBGA说起,说说PBGA的返修。
2. BGA器件的返修流程
BGA返修主要有下述几个步骤:准备、拆卸、植球、焊接和检测。
3.1准备:
烘干:这个是最容易让人忽视的程序,但恰恰也是十分重要和关键的程序。电路板和芯片烘干的主要目的是将潮气去除,否则由于焊接时的迅速升温,会使芯片内和电路板的潮气马上气化导致芯片损坏。而烘干后的板子要在 24小时内完成拆卸焊接,同时植球前的芯片也要保证是烘干过的,并且24小时内完成植球。注意烘板前,将温度敏感组件拆下后进行烘烤,例如光纤、电池、塑胶类拉手条等;否则容易造成的器件受热损伤。
产品保护:这个环节也容易被忽视,但也很重要。返修板正面、背面有光纤、附件区域的电池需要拆除后才可返修,若返修单板背面距离返修芯片10mm及10mm以外有散热器、插装晶振、电解电容、塑胶导光柱、非高温条形码、BGA、BGA插座等,须在其表面贴5-6层高温胶纸进行保护。
喷嘴和支撑的准备:对于宽度大于100mm的板子,应该给工作站加热台加支撑,支撑杆位置优选位于PCB板中间,使PCB保持平面,不能支撑到器件上。喷嘴选用实际尺寸比BGA大2~5mm的喷嘴。
拆卸/焊接曲线:由于加热中BGA锡球的实际温度与BGA的尺寸、封装材料、设备的加热系统效率、PCB的大小厚度以至于PCB在工作站的位置都有很大的关系,所以如果电脑中存储了返修曲线程序,那么每次拆卸/焊接前都要测量一下,如果没有程序则需要制作温度曲线。温度曲线板的制作规则和SMT的回流温度曲线板的制作过程是类似,采用一块与返修的PCB相同的试验板,对于BGA元件,要采取底部打孔,把热电偶伸进接触到BGA锡球,然后用高温锡或环氧树脂固定,见下图3。
SMT回流焊接工艺中一般使用两种常见类型的温度曲线,它们通常叫做保温型(平台型)和帐篷型(三角型)温度曲线。在保温型曲线中,装配在一段时间内经历相同的温度。帐篷型温度曲线是一个连续的温度上升,从装配进入炉子开始,直到装配达到所希望的峰值温度。返修工作站不同于回流炉,温区有限,想做成平台型的曲线比较困难,所以一般都是采用三角型的曲线。注意控制升温斜率在3度/秒以下;也要注意冷却斜率,冷却快,锡点强度会稍微大一点,但不可以太快而引起元件内部的温度应力,一般冷却斜率不大于5度/秒。制作曲线的关键是要对PCB的底部进行充分的预热,以防止翘曲;回流时间和最大温度就参考推荐的参数即可。图4是工作站测的一条无铅BGA温度曲线。
3.2拆卸:
在返修准备工作做好的情况下,拆卸工作比较容易,只需选择相应的温度曲线程序。拆卸程序运行中,根据BGA封装的物理特性,所有的焊点均位于封装体与PCB之间,焊点的加热熔化主要通过封装体与PCB的热传导。返修程序运行完毕后,由设备自动吸取被拆器件,当器件表面粗糙不平情况下允许采用镊子夹取;采用镊子夹取时,先用镊子轻轻拨动器件,确定器件已经完全融化后立即夹起。见图5
拆卸后,在BGA芯片植球和贴装之前,应清理返修区域,包括BGA焊盘和PCB焊盘。清理焊盘一般用扁平烙铁头+吸锡编带(如图6)。吸锡编带专门用于从BGA焊盘和元件上去除残留焊膏,不会损坏阻焊膜或暴露在外的印制线。将吸锡编带放置在基板与烙铁头之间,加热2至3秒钟,热量通过编带以最佳方式传递到焊点,然后向上抬起编带和烙铁,抬起而不是拖曳编织带,可使焊盘遭到损坏的危险降至最低。编织带可去除所有的残留焊锡,从而排除了桥接和短路的可能性。去除残留焊锡以后,用适当的溶剂清洗焊盘区域。
3.3植球:
经过拆卸的BGA器件一般情况下可以重复使用,但由于拆卸后BGA底部的焊球被不同程度的破坏,因此必须进行植球处理后才能使用。
锡球和辅料的选择:
植球使用的辅料选择很重要,目前主要使用的焊锡膏和助焊膏,使用助焊膏时,置完球的芯片加热过程中,在热风的工作站环境下锡球往往容易连桥,所以推荐选用锡膏来进行植球。
而锡球则根据芯片的datasheet来进行选择,成份上主要有无铅305、有铅63/37和CBGA用到的90Pb/10Sn等几种,大小主要有0.3、0.4、0.5、0.6和0.7mm几种。需要注意的是在选择锡膏工艺时,锡膏的成份要与锡球的成份一致,而且在锡球大小的选择上,要比原始芯片的直径小一些,这样锡球和锡膏重新融合成锡球后会最接近于原始芯片的大小。
植球的几种常用方法:根据植球工具和材料的不同,植球的方法也不相同,但工艺流程是相同的。即印刷焊膏--置球—加热。植球方法的区别在于第二步的置球。目前比较通用的置球方式有三种。
a.多用途植球器
此种植球器使用时,需要根据芯片的球径和球间距选择相应的模板,模板的开口尺寸一般比锡球直径大0.05-0.1mm,将模板固定在底座上,锡球均匀的撒在模板上,摇晃植球器,多余的锡球从模板上滚到锡球收集槽中,使模板表面恰好每个漏孔中保留一个锡球(图7图8)。然后把植球器放置在返修工作站上,把印刷好锡膏的BGA器件吸在工作站的吸嘴上(印好锡膏的焊盘面向下),按照焊接BGA的方法进行对中,使BGA器件底部图像与植球器模板表面每个锡球图像完全重合。然后将吸嘴向下移动,把BGA器件贴装到植球器模板的表面的锡球上(图9),将BGA器件吸起来,锡球将粘在BGA器件相应的焊盘上(图10),小心用镊子取下器件,进行后续的加热。此种植球的优点是模板利用率高,只需准备4片不同规格的模板即可满足绝大多数类型BGA的植球。缺点是操作稍显复杂,需要借助工作站的视觉对中系统,而且大批量植球时效率不高。
b.专用植球器
专用植球器(图11)需要根据芯片的DATASHEET进行制作,一个装载BGA器件的底座(图12),加上镶嵌印刷网板的盖板和镶嵌漏球模板的盖板各一个(图13)。使用时,首先印刷网板的盖板装载到装载有BGA的底座上,印刷锡膏后,取下盖板,然后把漏球模板的盖板装载到底座上,将锡球均匀的撒在模板上,摇晃植球器,多余的锡球从模板上滚到锡球收集槽中,使模板表面恰好每个漏孔中保留一个锡球。垂直取下盖板,观察BGA器件上有无缺少锡球的现象,用镊子补齐锡球。此种植球的优点是植球操作简单,成功率高,缺点是植球工装成本比较高,需要对每种不同封装的BGA器件制作一套。
c.万能植球器
此种万能植球器(图14)原理和专用植球器类似,区别就是此种植球器底座可以通过三个丝杆控制X和Y方向的宽度以及Z方向的高度,从而适合绝大多数BGA芯片。固定好芯片后(图15),后续的流程和专用植球器完全相同。如果维修不同封装的BGA,只需要制作相应的印刷网板和漏球网板,然后把网板放入盖板适配器上(图16),进行对位调整到合适位置锁紧即可。
上述三种植球方法,各有优缺点。不管采用哪种植球方法,后续的工作都要放到一个托板上,进行回流焊接。焊接时BGA器件的锡球面向上,需要注意的是热风量调到最小,以免把锡球吹移位,温度设定也比实际焊接温度要低一些,同时适时观察锡球熔化的状态,融融状态下持续十几秒就要停止加热,减少对芯片的热冲击。
3.4焊接:
焊接辅料的选择:无论是焊接新BGA还是植球后的BGA,对辅料的选择都是很严格的。焊接辅料主要有助焊膏和焊锡膏两种。两种辅料各有特点,助焊膏方式不需要制作钢网,涂覆简单快捷,维修速度快,但稳定性差,尤其对于大尺寸BGA容易产生开路等缺陷;而焊锡膏方式需要制作钢网,对印刷要求一定的技巧,但可以有效地补偿加热过程中由于PCB变形产生的翘曲,有效防止开路的产生,改善焊接效果,得到比用助焊膏焊接更好的效果。
对于CBGA,由于锡球是高温的90Pb/10Sn,熔点为302℃,焊接过程不熔化,故返修过程必须涂覆焊锡膏。
通过对实际焊接过程的分析及对焊接结果的观察统计,在PCB上涂覆焊锡膏具有稳定性高,减少焊接缺陷,补偿PCB热变形等助焊膏不具备的优点,所以在实际焊接过程中,给出如下建议。在BGA尺寸大于15mm*15mm时和BGA是CBGA封装条件下,必须使用焊锡膏作为焊接辅料;在BGA尺寸小于15mm*15mm,且PCB厚度大于等于1.6mm时,如果对维修速度要求较高,可以考虑使用助焊膏。
BGA焊接的流程:印刷锡膏(助焊膏)-视觉对中-回流
a. 印刷锡膏(助焊膏)
涂覆助焊膏:用画笔蘸少许助焊膏,在焊盘上来回轻轻涂抹,检查焊盘上助焊膏的涂抹情况,要求助焊膏涂布均匀。不可有助焊膏堆积现象,焊盘上不可有纤维、毛发等残留。
印刷锡膏:印刷锡膏使用的钢网有两种类型,簸箕型(图17)和钢片型(图18),两种类型应用都很普遍,网板的厚度和开孔的选择与SMT生产钢网的规范一致,依据锡球直径和间距的大小。下面以钢片型钢网为例,说说印刷锡膏的流程。选择对应的印锡钢网,将印锡的小钢网定位并用胶带粘贴在PCB上(用来固定钢网,并防止锡膏外溢);需要使钢网开口和焊盘完全重合,不错位。用刮刀取适量锡膏,然后在小钢网上刮过。刮锡膏时尽量使锡膏能在钢网和刮刀之间滚动(图19图20)。然后向上慢慢的提起钢网,提取的过程中,要减少手的抖动。
b.视觉对中
将涂抹好锡膏的单板平稳放置在工作台上,将器件放在机器喷口中的吸嘴上,注意方向,然后进行视觉对中(图21),使器件和焊盘的影像重合(图22),运行机器,完成贴放动作。(采用印锡返修时,必须使用设备将BGA贴放在PCB上,不得使用手工放置。采用刷助焊膏返修时,可以用手工放置器件,以丝印框为准进行对位)。器件贴放后,需要检查返修器件的高度是否一致,是否有高度不平、器件倾斜等异常。
c.回流
贴装检查完毕后,选择与芯片对应的温度曲线程序对BGA进行加热,程序运行完毕,完成器件焊接过程。待板子冷却后取走PCB。
3.5 检测:
由于BGA焊点是不可见焊点,所以除了电性能测试外,主要应用X射线检测。X射线透视图可显示焊接厚度、形状及质量的密度分布。厚度与形状不仅是反映长期结构质量的指标,在测定开路、冷焊(图23)、短路(图24)缺陷及焊接不足方面,也是很好的指标。
3. BGA返修常见问题分析
芯片翘曲:
BGA出现焊接缺陷后,如果进行拆卸植球焊接,总共经历了SMT回流,拆卸,焊盘清理,植球,焊接等至少5次的热冲击,接近了极限的寿命,统计发现最终有5% 的BGA芯片会有翘曲分层,所以在这几个环节中一定要注意控制芯片的受热,拆卸和焊盘清理和植球环节中尽量降低温度和减少加热时间。
PCB翘曲:
热风工作站采用上下部同时局部加热来完成BGA的焊接,由于PCB材质的热胀冷缩性质和PCB本身的重力作用,因而对PCB中BGA区域产生更大的热应力,会使得PCB在返修过程中产生一定程度上的翘曲变形,支撑虽然起了一定的作用,但PCB变形仍然存在。严重时这种变形会导致外部连接点与焊盘的接触减至最小,进而产生BGA四角焊点桥接,中间焊接空焊等焊接缺陷。因此要尽量控制温度,由于工作站底部加热面积较大,在保证曲线最大温度和回流时间条件下,增加预热时间,提高底部加热温度,而降低顶部加热温度,会大大的减少PCB的热变形;另外就是注意底部支撑放置的位置和高度。
焊接开路:
造成焊接开路的原因比较复杂,上面论述的PCB翘曲是一个原因。另外还有几个因素可能导致开路,重点查看焊接曲线是否正确,不正确的曲线会导致回流时间过短或温度过低,而锡球和锡膏没有充分回流造成开路;是否因为采用了助焊膏而不是焊锡膏作为焊接辅料,使用焊锡膏回流制程,发生开路的可能性会减少,这是因为焊锡膏对共面性的要求较低;是否PCB和芯片焊接前没有进行烘干等等。
焊接短路:
PCB翘曲是导致焊接短路的原因之一,其他原因还有,网板开孔的厚度和印刷的锡膏量是否合适,锡膏过厚且不均匀,极容易产生短路;PCB和芯片是否烘干,如果没有烘干,爆米花现象将可能引起短路;清理焊盘时是否破坏了阻焊膜,如果阻焊被破坏,很容易导致短路;另外就是温度曲线是否正确。
4. 综述
不管BGA返修技术怎么发展,返修效果如何的好,芯片在多次受到热冲击条件下,仍然存在着寿命缩短,稳定性变差的隐患,所以在提高返修能力的基础上,还要从前端SMT环节,通过制程优化、设备和人员物料等管理环节,减少BGA的返修,从而达到高合格率,使BGA更具成本效益。
目前BGA的生产制程也很稳定,每家公司也都在提高工艺水平加强管理,BGA缺陷率也在逐步降低,但百密也有一疏,不可能完全杜绝BGA返修。所以每家公司适当地培训返修技术人员,采用恰当的返修设备,了解BGA返修的关键工序,并且不断总结返修的经验,优化返修的制程,改进返修工艺,这些都有助于实现稳定、有效的返修。
关键词: PBGA,CBGA,温度曲线,助焊膏,植球,翘曲
1. BGA器件的分类和特点
说起BGA的返修,首先我们先了解一下这种器件的特点。BGA封装的I/O端子以圆形或柱状焊点按阵列形式分布在封装下面,焊点的加热熔化主要通过封装体与PCB的热传导。
BGA主要有PBGA,CBGA,CCGA和TBGA几大类,我们目前生产中比较常见的是PBGA和CBGA。
PBGA (plastic BGA)是塑料封装的BGA(见图1),也是目前使用较多的BGA,它使用63/37(有铅)或者305(无铅)成分的焊锡球,焊锡的熔化温度为183℃或者217℃。PBGA的优点是成本较低,容易加工,不过由于塑料封装,容易吸潮。

CBGA(ceramic BGA)是陶瓷封装的BGA(见图2),也有一定范围的应用,CBGA焊球的成分为90Pb/10Sn(它与PCB连接处的焊锡成分仍为63Sn/37Pb)。CBGA是在元件和印制板上采用不熔焊球(实际上是它的熔点大大高于回流焊的温度),焊球直径为0.889mm,高度保持不变。CBGA的焊锡球较PBGA不容易吸潮,且封装的更牢靠,CBGA芯片底部焊点直径要比PCB上的焊盘大,拆除CBGA芯片后,焊锡不会在PCB的焊盘上。
BGA与其他类型元件的区别就是焊点在元件本体的下部,不能够通过烙铁等常规工具进行拆卸焊接,而且拆卸焊接过程也不能够看到焊点的熔化和固化过程。这就决定了BGA维修的特殊性。下面我们就从上述应用最广泛的PBGA说起,说说PBGA的返修。
2. BGA器件的返修流程
BGA返修主要有下述几个步骤:准备、拆卸、植球、焊接和检测。
3.1准备:
烘干:这个是最容易让人忽视的程序,但恰恰也是十分重要和关键的程序。电路板和芯片烘干的主要目的是将潮气去除,否则由于焊接时的迅速升温,会使芯片内和电路板的潮气马上气化导致芯片损坏。而烘干后的板子要在 24小时内完成拆卸焊接,同时植球前的芯片也要保证是烘干过的,并且24小时内完成植球。注意烘板前,将温度敏感组件拆下后进行烘烤,例如光纤、电池、塑胶类拉手条等;否则容易造成的器件受热损伤。
产品保护:这个环节也容易被忽视,但也很重要。返修板正面、背面有光纤、附件区域的电池需要拆除后才可返修,若返修单板背面距离返修芯片10mm及10mm以外有散热器、插装晶振、电解电容、塑胶导光柱、非高温条形码、BGA、BGA插座等,须在其表面贴5-6层高温胶纸进行保护。
喷嘴和支撑的准备:对于宽度大于100mm的板子,应该给工作站加热台加支撑,支撑杆位置优选位于PCB板中间,使PCB保持平面,不能支撑到器件上。喷嘴选用实际尺寸比BGA大2~5mm的喷嘴。
拆卸/焊接曲线:由于加热中BGA锡球的实际温度与BGA的尺寸、封装材料、设备的加热系统效率、PCB的大小厚度以至于PCB在工作站的位置都有很大的关系,所以如果电脑中存储了返修曲线程序,那么每次拆卸/焊接前都要测量一下,如果没有程序则需要制作温度曲线。温度曲线板的制作规则和SMT的回流温度曲线板的制作过程是类似,采用一块与返修的PCB相同的试验板,对于BGA元件,要采取底部打孔,把热电偶伸进接触到BGA锡球,然后用高温锡或环氧树脂固定,见下图3。
SMT回流焊接工艺中一般使用两种常见类型的温度曲线,它们通常叫做保温型(平台型)和帐篷型(三角型)温度曲线。在保温型曲线中,装配在一段时间内经历相同的温度。帐篷型温度曲线是一个连续的温度上升,从装配进入炉子开始,直到装配达到所希望的峰值温度。返修工作站不同于回流炉,温区有限,想做成平台型的曲线比较困难,所以一般都是采用三角型的曲线。注意控制升温斜率在3度/秒以下;也要注意冷却斜率,冷却快,锡点强度会稍微大一点,但不可以太快而引起元件内部的温度应力,一般冷却斜率不大于5度/秒。制作曲线的关键是要对PCB的底部进行充分的预热,以防止翘曲;回流时间和最大温度就参考推荐的参数即可。图4是工作站测的一条无铅BGA温度曲线。

在返修准备工作做好的情况下,拆卸工作比较容易,只需选择相应的温度曲线程序。拆卸程序运行中,根据BGA封装的物理特性,所有的焊点均位于封装体与PCB之间,焊点的加热熔化主要通过封装体与PCB的热传导。返修程序运行完毕后,由设备自动吸取被拆器件,当器件表面粗糙不平情况下允许采用镊子夹取;采用镊子夹取时,先用镊子轻轻拨动器件,确定器件已经完全融化后立即夹起。见图5

3.3植球:
经过拆卸的BGA器件一般情况下可以重复使用,但由于拆卸后BGA底部的焊球被不同程度的破坏,因此必须进行植球处理后才能使用。
锡球和辅料的选择:
植球使用的辅料选择很重要,目前主要使用的焊锡膏和助焊膏,使用助焊膏时,置完球的芯片加热过程中,在热风的工作站环境下锡球往往容易连桥,所以推荐选用锡膏来进行植球。
而锡球则根据芯片的datasheet来进行选择,成份上主要有无铅305、有铅63/37和CBGA用到的90Pb/10Sn等几种,大小主要有0.3、0.4、0.5、0.6和0.7mm几种。需要注意的是在选择锡膏工艺时,锡膏的成份要与锡球的成份一致,而且在锡球大小的选择上,要比原始芯片的直径小一些,这样锡球和锡膏重新融合成锡球后会最接近于原始芯片的大小。
植球的几种常用方法:根据植球工具和材料的不同,植球的方法也不相同,但工艺流程是相同的。即印刷焊膏--置球—加热。植球方法的区别在于第二步的置球。目前比较通用的置球方式有三种。
a.多用途植球器
此种植球器使用时,需要根据芯片的球径和球间距选择相应的模板,模板的开口尺寸一般比锡球直径大0.05-0.1mm,将模板固定在底座上,锡球均匀的撒在模板上,摇晃植球器,多余的锡球从模板上滚到锡球收集槽中,使模板表面恰好每个漏孔中保留一个锡球(图7图8)。然后把植球器放置在返修工作站上,把印刷好锡膏的BGA器件吸在工作站的吸嘴上(印好锡膏的焊盘面向下),按照焊接BGA的方法进行对中,使BGA器件底部图像与植球器模板表面每个锡球图像完全重合。然后将吸嘴向下移动,把BGA器件贴装到植球器模板的表面的锡球上(图9),将BGA器件吸起来,锡球将粘在BGA器件相应的焊盘上(图10),小心用镊子取下器件,进行后续的加热。此种植球的优点是模板利用率高,只需准备4片不同规格的模板即可满足绝大多数类型BGA的植球。缺点是操作稍显复杂,需要借助工作站的视觉对中系统,而且大批量植球时效率不高。

专用植球器(图11)需要根据芯片的DATASHEET进行制作,一个装载BGA器件的底座(图12),加上镶嵌印刷网板的盖板和镶嵌漏球模板的盖板各一个(图13)。使用时,首先印刷网板的盖板装载到装载有BGA的底座上,印刷锡膏后,取下盖板,然后把漏球模板的盖板装载到底座上,将锡球均匀的撒在模板上,摇晃植球器,多余的锡球从模板上滚到锡球收集槽中,使模板表面恰好每个漏孔中保留一个锡球。垂直取下盖板,观察BGA器件上有无缺少锡球的现象,用镊子补齐锡球。此种植球的优点是植球操作简单,成功率高,缺点是植球工装成本比较高,需要对每种不同封装的BGA器件制作一套。

此种万能植球器(图14)原理和专用植球器类似,区别就是此种植球器底座可以通过三个丝杆控制X和Y方向的宽度以及Z方向的高度,从而适合绝大多数BGA芯片。固定好芯片后(图15),后续的流程和专用植球器完全相同。如果维修不同封装的BGA,只需要制作相应的印刷网板和漏球网板,然后把网板放入盖板适配器上(图16),进行对位调整到合适位置锁紧即可。

3.4焊接:
焊接辅料的选择:无论是焊接新BGA还是植球后的BGA,对辅料的选择都是很严格的。焊接辅料主要有助焊膏和焊锡膏两种。两种辅料各有特点,助焊膏方式不需要制作钢网,涂覆简单快捷,维修速度快,但稳定性差,尤其对于大尺寸BGA容易产生开路等缺陷;而焊锡膏方式需要制作钢网,对印刷要求一定的技巧,但可以有效地补偿加热过程中由于PCB变形产生的翘曲,有效防止开路的产生,改善焊接效果,得到比用助焊膏焊接更好的效果。
对于CBGA,由于锡球是高温的90Pb/10Sn,熔点为302℃,焊接过程不熔化,故返修过程必须涂覆焊锡膏。
通过对实际焊接过程的分析及对焊接结果的观察统计,在PCB上涂覆焊锡膏具有稳定性高,减少焊接缺陷,补偿PCB热变形等助焊膏不具备的优点,所以在实际焊接过程中,给出如下建议。在BGA尺寸大于15mm*15mm时和BGA是CBGA封装条件下,必须使用焊锡膏作为焊接辅料;在BGA尺寸小于15mm*15mm,且PCB厚度大于等于1.6mm时,如果对维修速度要求较高,可以考虑使用助焊膏。
BGA焊接的流程:印刷锡膏(助焊膏)-视觉对中-回流
a. 印刷锡膏(助焊膏)
涂覆助焊膏:用画笔蘸少许助焊膏,在焊盘上来回轻轻涂抹,检查焊盘上助焊膏的涂抹情况,要求助焊膏涂布均匀。不可有助焊膏堆积现象,焊盘上不可有纤维、毛发等残留。
印刷锡膏:印刷锡膏使用的钢网有两种类型,簸箕型(图17)和钢片型(图18),两种类型应用都很普遍,网板的厚度和开孔的选择与SMT生产钢网的规范一致,依据锡球直径和间距的大小。下面以钢片型钢网为例,说说印刷锡膏的流程。选择对应的印锡钢网,将印锡的小钢网定位并用胶带粘贴在PCB上(用来固定钢网,并防止锡膏外溢);需要使钢网开口和焊盘完全重合,不错位。用刮刀取适量锡膏,然后在小钢网上刮过。刮锡膏时尽量使锡膏能在钢网和刮刀之间滚动(图19图20)。然后向上慢慢的提起钢网,提取的过程中,要减少手的抖动。
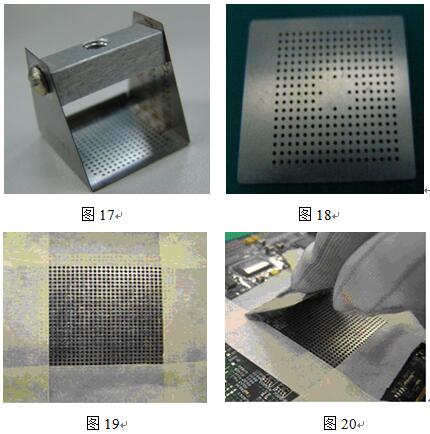
将涂抹好锡膏的单板平稳放置在工作台上,将器件放在机器喷口中的吸嘴上,注意方向,然后进行视觉对中(图21),使器件和焊盘的影像重合(图22),运行机器,完成贴放动作。(采用印锡返修时,必须使用设备将BGA贴放在PCB上,不得使用手工放置。采用刷助焊膏返修时,可以用手工放置器件,以丝印框为准进行对位)。器件贴放后,需要检查返修器件的高度是否一致,是否有高度不平、器件倾斜等异常。
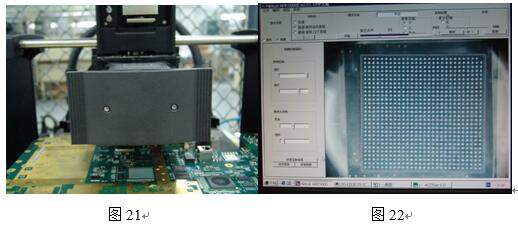
贴装检查完毕后,选择与芯片对应的温度曲线程序对BGA进行加热,程序运行完毕,完成器件焊接过程。待板子冷却后取走PCB。
3.5 检测:
由于BGA焊点是不可见焊点,所以除了电性能测试外,主要应用X射线检测。X射线透视图可显示焊接厚度、形状及质量的密度分布。厚度与形状不仅是反映长期结构质量的指标,在测定开路、冷焊(图23)、短路(图24)缺陷及焊接不足方面,也是很好的指标。

3. BGA返修常见问题分析
芯片翘曲:
BGA出现焊接缺陷后,如果进行拆卸植球焊接,总共经历了SMT回流,拆卸,焊盘清理,植球,焊接等至少5次的热冲击,接近了极限的寿命,统计发现最终有5% 的BGA芯片会有翘曲分层,所以在这几个环节中一定要注意控制芯片的受热,拆卸和焊盘清理和植球环节中尽量降低温度和减少加热时间。
PCB翘曲:
热风工作站采用上下部同时局部加热来完成BGA的焊接,由于PCB材质的热胀冷缩性质和PCB本身的重力作用,因而对PCB中BGA区域产生更大的热应力,会使得PCB在返修过程中产生一定程度上的翘曲变形,支撑虽然起了一定的作用,但PCB变形仍然存在。严重时这种变形会导致外部连接点与焊盘的接触减至最小,进而产生BGA四角焊点桥接,中间焊接空焊等焊接缺陷。因此要尽量控制温度,由于工作站底部加热面积较大,在保证曲线最大温度和回流时间条件下,增加预热时间,提高底部加热温度,而降低顶部加热温度,会大大的减少PCB的热变形;另外就是注意底部支撑放置的位置和高度。
焊接开路:
造成焊接开路的原因比较复杂,上面论述的PCB翘曲是一个原因。另外还有几个因素可能导致开路,重点查看焊接曲线是否正确,不正确的曲线会导致回流时间过短或温度过低,而锡球和锡膏没有充分回流造成开路;是否因为采用了助焊膏而不是焊锡膏作为焊接辅料,使用焊锡膏回流制程,发生开路的可能性会减少,这是因为焊锡膏对共面性的要求较低;是否PCB和芯片焊接前没有进行烘干等等。
焊接短路:
PCB翘曲是导致焊接短路的原因之一,其他原因还有,网板开孔的厚度和印刷的锡膏量是否合适,锡膏过厚且不均匀,极容易产生短路;PCB和芯片是否烘干,如果没有烘干,爆米花现象将可能引起短路;清理焊盘时是否破坏了阻焊膜,如果阻焊被破坏,很容易导致短路;另外就是温度曲线是否正确。
4. 综述
不管BGA返修技术怎么发展,返修效果如何的好,芯片在多次受到热冲击条件下,仍然存在着寿命缩短,稳定性变差的隐患,所以在提高返修能力的基础上,还要从前端SMT环节,通过制程优化、设备和人员物料等管理环节,减少BGA的返修,从而达到高合格率,使BGA更具成本效益。
目前BGA的生产制程也很稳定,每家公司也都在提高工艺水平加强管理,BGA缺陷率也在逐步降低,但百密也有一疏,不可能完全杜绝BGA返修。所以每家公司适当地培训返修技术人员,采用恰当的返修设备,了解BGA返修的关键工序,并且不断总结返修的经验,优化返修的制程,改进返修工艺,这些都有助于实现稳定、有效的返修。
版权所有 ©深圳市亚中咨询有限公司
电话:0755-25856945 邮箱:pzl88smt@126.com 网址:www.smt668.com
地址:深圳市罗湖区怡正发大厦 SMT专业网版权所有(c) 2010 粤ICP备17073069号
本站部分图文来源网络,如有侵权问题请通知我们处理!
网站建设维护